Alles, was schwingt
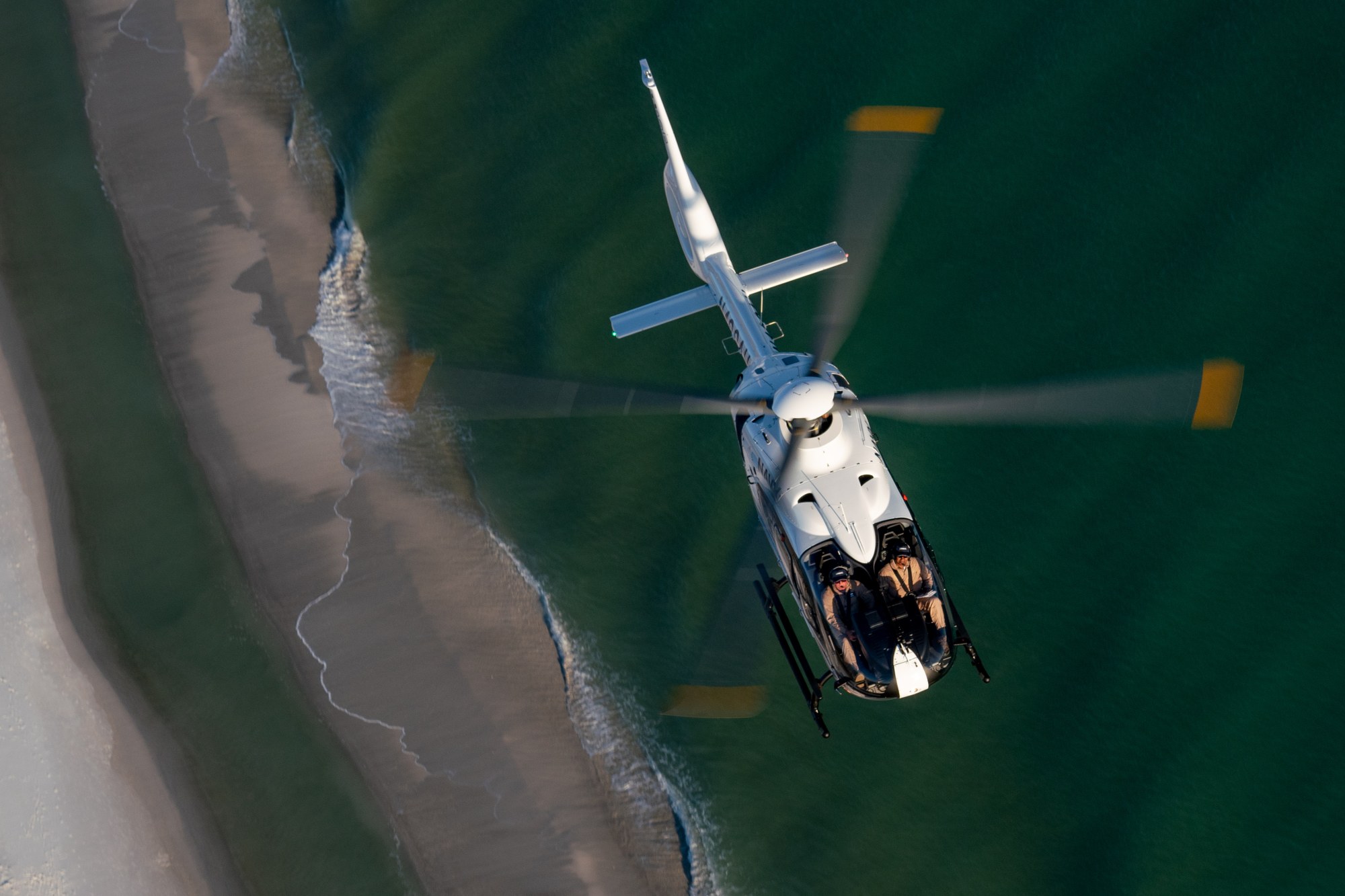
Jonny CAROLL 2018
Ob bei der Bergrettung, bei der Brandbekämpfung oder bei Polizeieinsätzen – Hubschrauber kommen in den verschiedensten Bereichen zum Einsatz. Im Gegensatz zu Flugzeugen können sie senkrecht starten und landen. Dank ihrer Leichtbauweise haben sie eine hohe Flugleistung und geringe Betriebskosten. Einen Nachteil bringen die wendigen Flieger jedoch mit sich: Aufgrund ihrer Leichtbaustruktur sind sie anfällig für mechanische Schwingungen. Starke Schwingungen erschweren die Bedienbarkeit des Hubschraubers und können bei Missionen wie heiklen Krankentransporten oder Luftaufklärungen mit hochauflösenden Kameras stören. Heute werden Hubschrauber zu großen Teilen am Computer entworfen. Die zugrunde liegenden Modelle müssen möglichst realitätsgetreu sein. Um das zu erreichen, begleiteten Forscherinnen und Forscher aus dem DLR-Institut für Aeroelastik den Bau eines Helikopters und untersuchten seine Teile Stück für Stück für Stück …
Wie Schwingungen sichtbar werden
Vibrationen entstehen infolge dynamischer Rotorlasten im Wesentlichen durch die Queranströmung des Hauptrotors und lassen sich deshalb nicht völlig vermeiden. Von dort können sie sich über die komplette Struktur des Fluggeräts ausbreiten. Um einen möglichst vibrationsarmen Hubschrauber zu entwickeln, müssen die Fachleute die entsprechenden Kräfte im Voraus berechnen. Heutzutage nutzen sie dazu computerbasierte Verfahren wie CFD oder MKS (siehe Glossar). Im zweiten Schritt simulieren die Entwicklerinnen und Entwickler den Einfluss der Schwingungen auf die Hubschrauberzelle. Das Simulationsprogramm zeigt, wie sich die Kräfte innerhalb der Zelle ausbreiten und an welchen Stellen die Vibrationen am größten sind. Auf Grundlage dieser Simulation werden dann Maßnahmen entwickelt, die die Vibrationen gezielt reduzieren. Allerdings sind die Modelle, die den Berechnungen zugrunde liegen, bislang noch nicht genau genug.
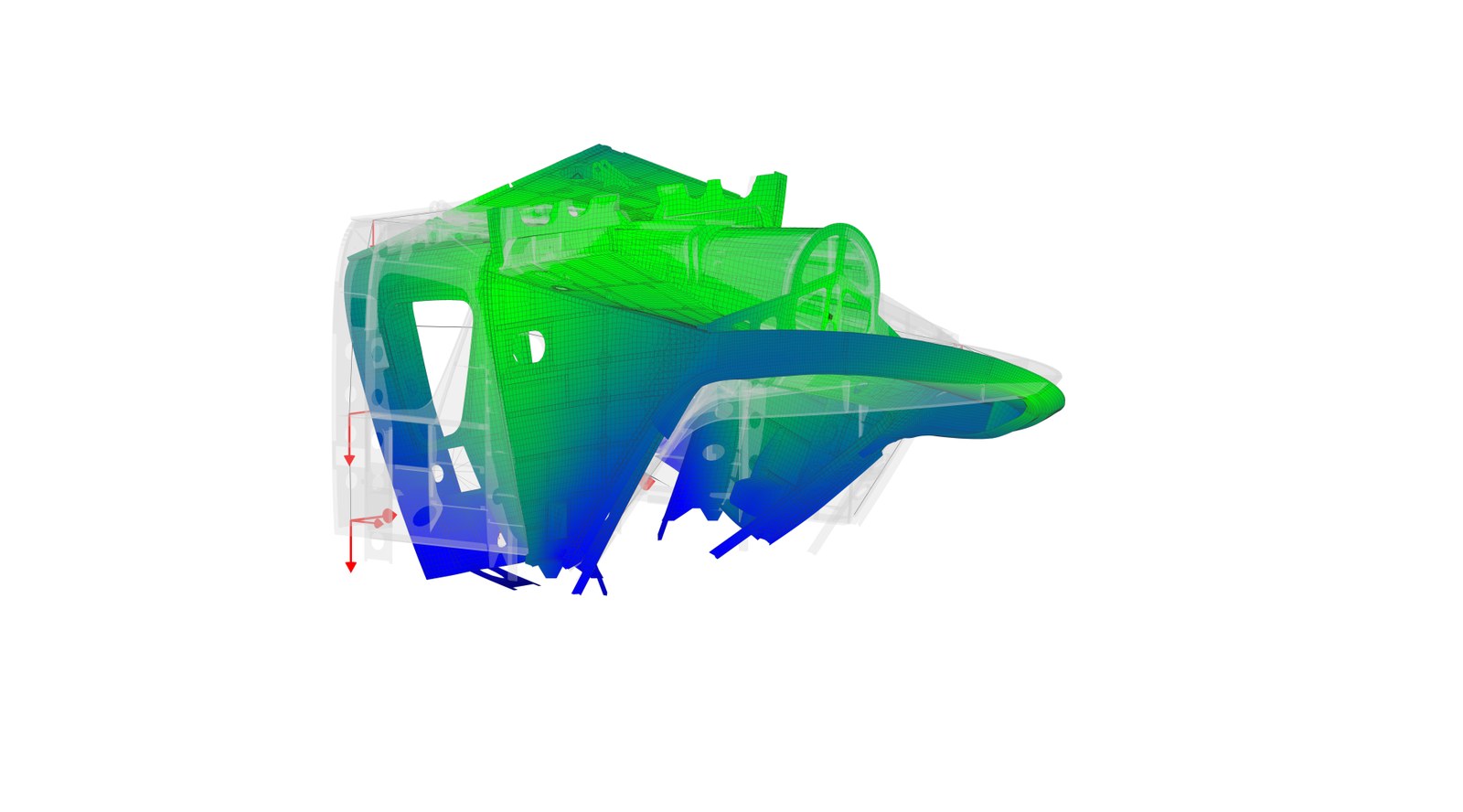
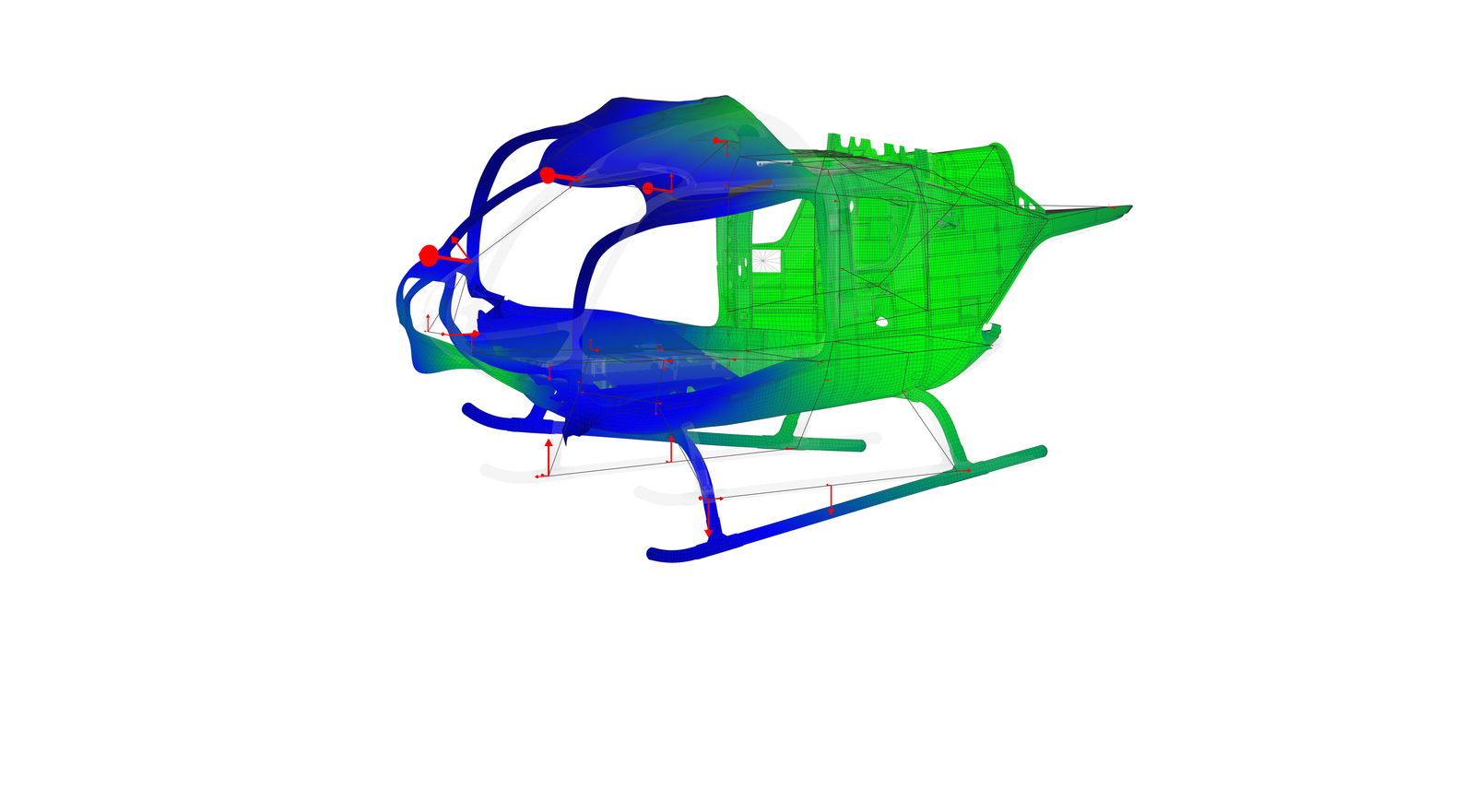
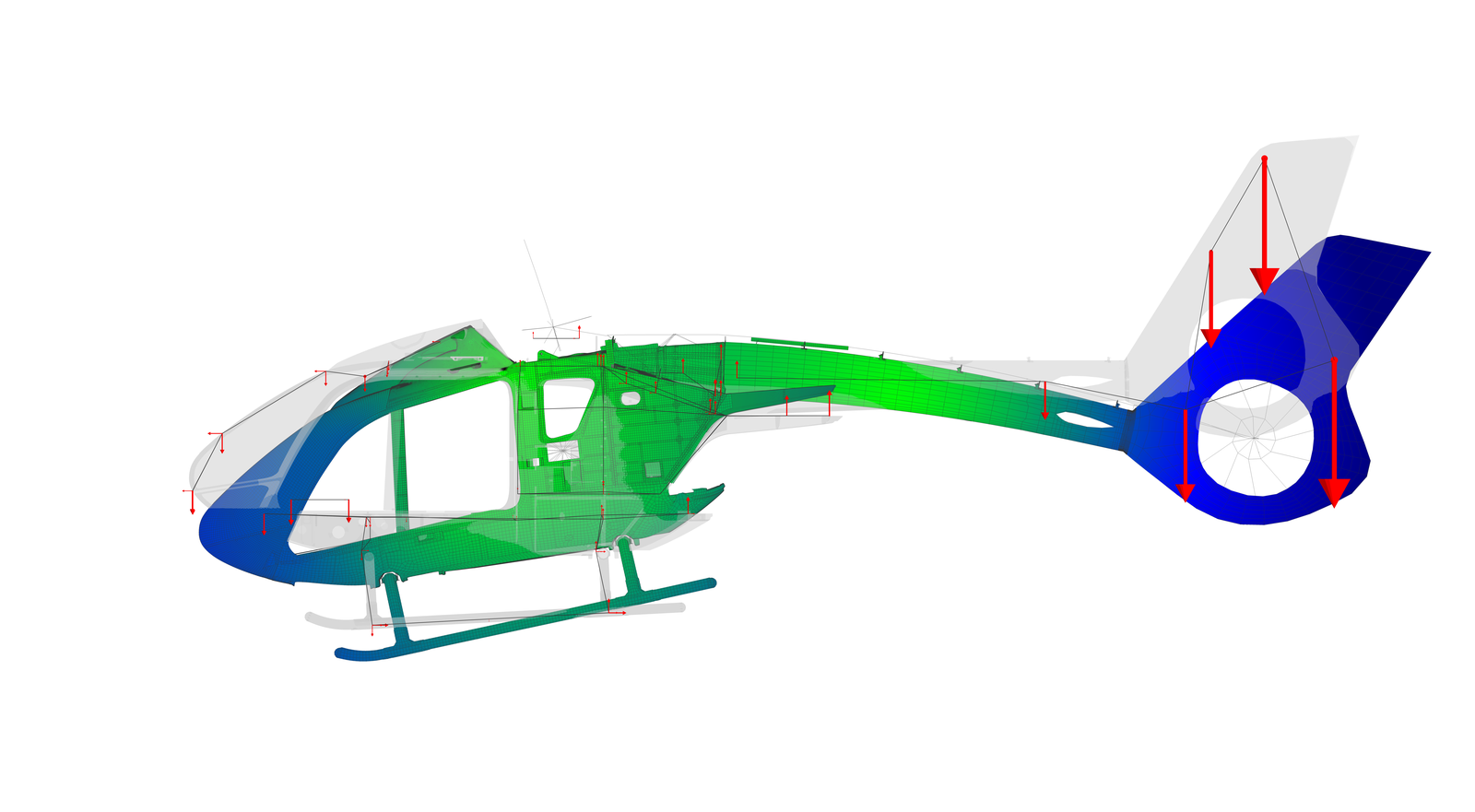
Das Ziel: ein Modell, ganz nah an der Realität
Im Projekt eVolve schlossen sich Forschende des DLR-Instituts für Aeroelastik sowie Entwicklerinnen und Entwickler von Airbus Helicopters Deutschland zusammen, um dies zu ändern. Ihr Ziel war es, digitale Hubschraubermodelle so zu verbessern, dass diese die Vibrationen so realitätsgetreu wie möglich abbilden. Solche Berechnungsmodelle werden bereits in der Entwurfsphase aufgebaut. Für den Aufbau der Berechnungsmodelle nutzen die Ingenieurinnen und Ingenieure CAD- und FEM-Modelle und treffen Annahmen zum mechanischen Verhalten der Konstruktion. Nach der Entwurfsphase bauen sie einen Prototyp. Im Standschwingungstest wird das strukturdynamische Verhalten untersucht. Die Ergebnisse des Tests vergleichen sie mit den Ergebnissen der FEM-Simulation. Sind die Abweichungen zwischen Test und Simulation zu groß, müssen die Berechnungsmodelle an die Realität angepasst werden. Ein vollständiger Hubschrauber ist sehr komplex und es gibt viele mögliche Stellen, an denen Abweichungen auftreten können. Diese sind meist auf unzureichende Annahmen des mechanischen Verhaltens zurückzuführen und werden durch den Vergleich mit Testdaten überprüft und verbessert.
Glossar
CFD-Verfahren: CFD steht für Computational Fluid Dynamics (Deutsch: numerische Verfahren zur Strömungsberechnung). Es ist die Umsetzung der Strömungsmechanik als Computerprogramm. Die zugrunde liegenden mathematischen Modelle sind die Navier-Stokes-Gleichungen, Euler-Gleichungen und Potenzialgleichungen.
MKS: Die Mehrkörpersimulation (MKS) bildet das Zusammenspiel mehrerer mechanischer Bauteile ab. Mithilfe dieser Computersimulation können die Forschenden komplizierte Bewegungsabläufe berechnen und dynamische Reaktionen oder die Leistung von beweglichen Bauteilen vorhersagen.
CAD: Beim CAD (Computer Aided Design) werden am Computer mithilfe entsprechender Software Entwürfe, Modelle, Konstruktionen und technische Zeichnungen erzeugt. Das vereinfacht die Konstruktion oder technische Zeichnungen.
FEM: Die Finite-Elemente-Methode (FEM) ist ein Verfahren, das häufig zur Beantwortung mechanischer Fragestellungen bei Strukturen mit komplexer Geometrie verwendet wird. Die Strukturen werden in kleinere Bereiche, sogenannte finite Elemente, unterteilt, für die sich leichter entsprechende Gleichungen aufstellen lassen.
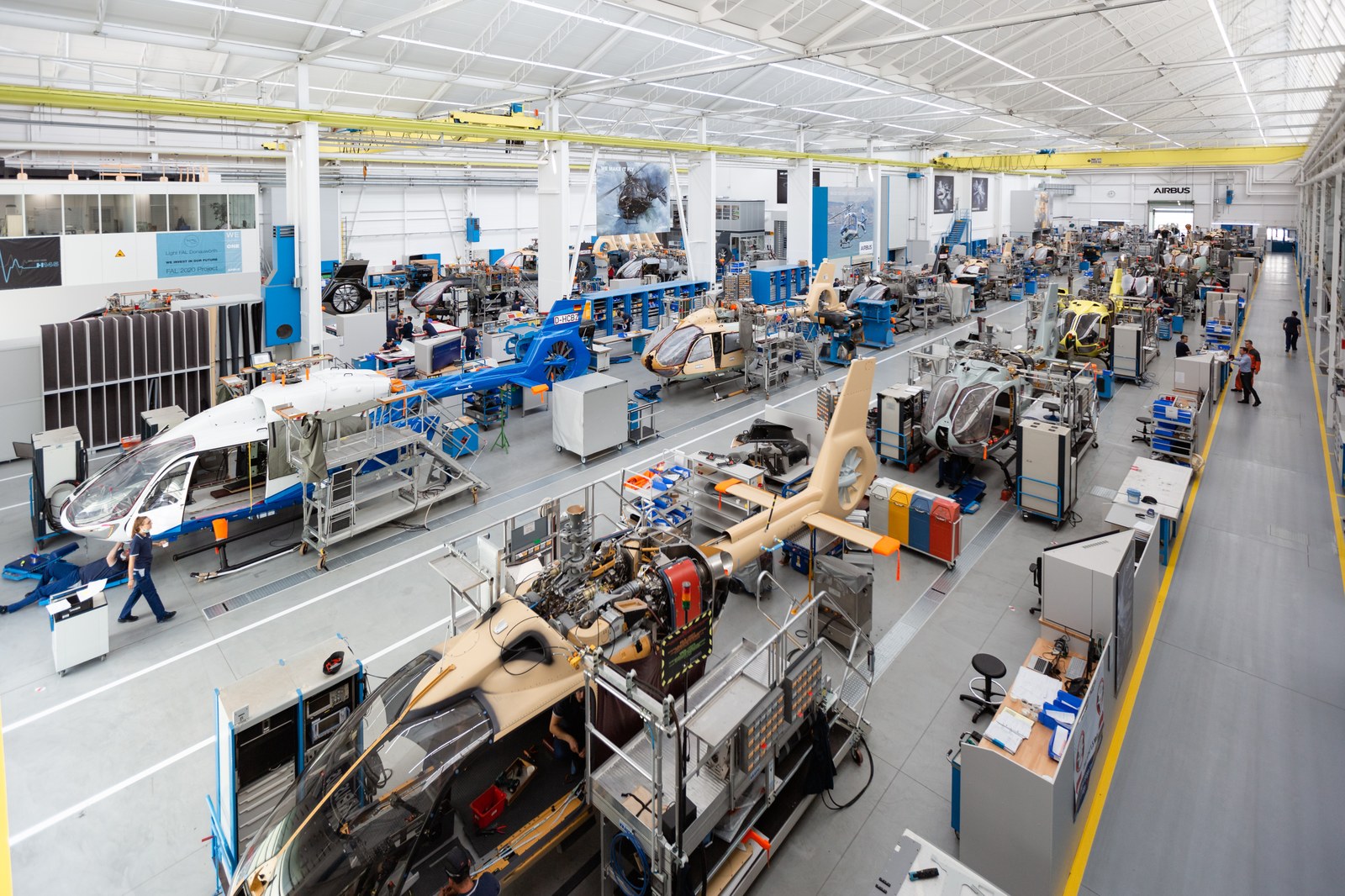
Airbus Helicopters
Im eVolve-Projekt untersuchte das Team einzelne Komponenten, die in der Montagelinie nach und nach zu einem kompletten Hubschrauber zusammengesetzt werden. Somit können Berechnungsfehler bereits frühzeitig und in kleineren Bauteilen erkannt werden. Sie testeten die Bauteile aber nicht etwa im Labor des DLR in Göttingen, sondern in Donauwörth. Hier werden die Helikopter von Airbus gebaut. Zunächst wählten sie einen Kandidaten, den sie über die ganze Fertigung begleiten würden. Dieser sollte möglichst repräsentativ sein. Sie entschieden sich für einen Helikopter ohne zusätzliche An- oder Aufbauten, denn mitunter sind die Fluggeräte neben der Basisausstattung noch mit Seilwinden, Radar, Kameras, Krankentragen oder Ähnlichem ausgerüstet.
Airbus Helicopters
Der Baufortschritt wirkt sich auf das Schwingungsverhalten eines Hubschraubers aus. An manchen Montagestationen ändern sich die Masse oder die Steifigkeit der Gesamtstruktur besonders stark. Deshalb sind diese strukturdynamisch besonders relevant. Hier führte das DLR-Team Messungen durch. „Für uns war es eine ganz besondere Situation, mitten im laufenden Fertigungsbetrieb Experimente zu machen. Normalerweise messen wir in einem Hangar beziehungsweise im Labor, wo wir alles kontrollieren können. Das war jetzt ein bisschen anders“, sagt Johannes Knebusch vom DLR-Institut für Aeroelastik.
An jeder Station musste sich das Team auf neue Situationen einstellen: Während die Forschenden die Vibration der Bauteile an der ersten Montagestation noch mit einem Impulshammer anregen konnten, weil es nur wenige Teile waren, mussten sie am Ende elektrodynamische Shaker einsetzen, wie sie auch für Vibrationsmessungen an großen Flugzeugen genutzt werden. Für die Experimente hing der Hubschrauber im jeweiligen Bauzustand weich an Gummiseilen. Die Seile gewährleisteten, dass stets dieselben Randbedingungen herrschten und die Ergebnisse miteinander vergleichbar waren. „Hinzu kam auch, dass wir den Fertigungsbetrieb mit unseren Experimenten nicht aufhalten wollten, was uns gut gelungen ist. Außerdem waren unsere Partner sehr flexibel, was die Arbeit extrem erleichtert hat“, ergänzt Marc Böswald, Abteilungsleiter im DLR-Institut für Aeroelastik.
Aus den Ergebnissen erstellten die Forschenden ein dynamisches Modell für den jeweiligen Bauzustand und verglichen es mit den vorhandenen Simulationsmodellen. Dadurch wurde sichtbar, wo in den Modellen Berechnungsfehler waren. Insgesamt führte das Team an zehn Montagestationen Messungen durch. Bei den ersten Tests setzten sie nur rund 30 Sensoren ein, an der letzten Station waren es schon mehr als 200.
Der Vergleich mit Testdaten bildet die Grundlage dafür, vorhandene Simulationsmodelle anzupassen und weiter zu verbessern. Ein weiterer Vorteil ist, dass Simulationen aus frühen Stadien Schwingungsformen einzelner Bauteile zeigen. Diese können dazu genutzt werden, gezielt Modellfehler in verschiedenen Baugruppen aufzuspüren. Später, wenn der komplette Helikopter getestet wird, sind diese Fehler nicht mehr erkennbar. In Zukunft möchte Airbus dieses Vorgehen auch bei anderen Hubschraubertypen anwenden, um auch deren Simulationsmodelle zu verbessern – ein weiterer wichtiger Schritt hin zur Entwicklung vibrationsarmer Hubschrauberzellen.
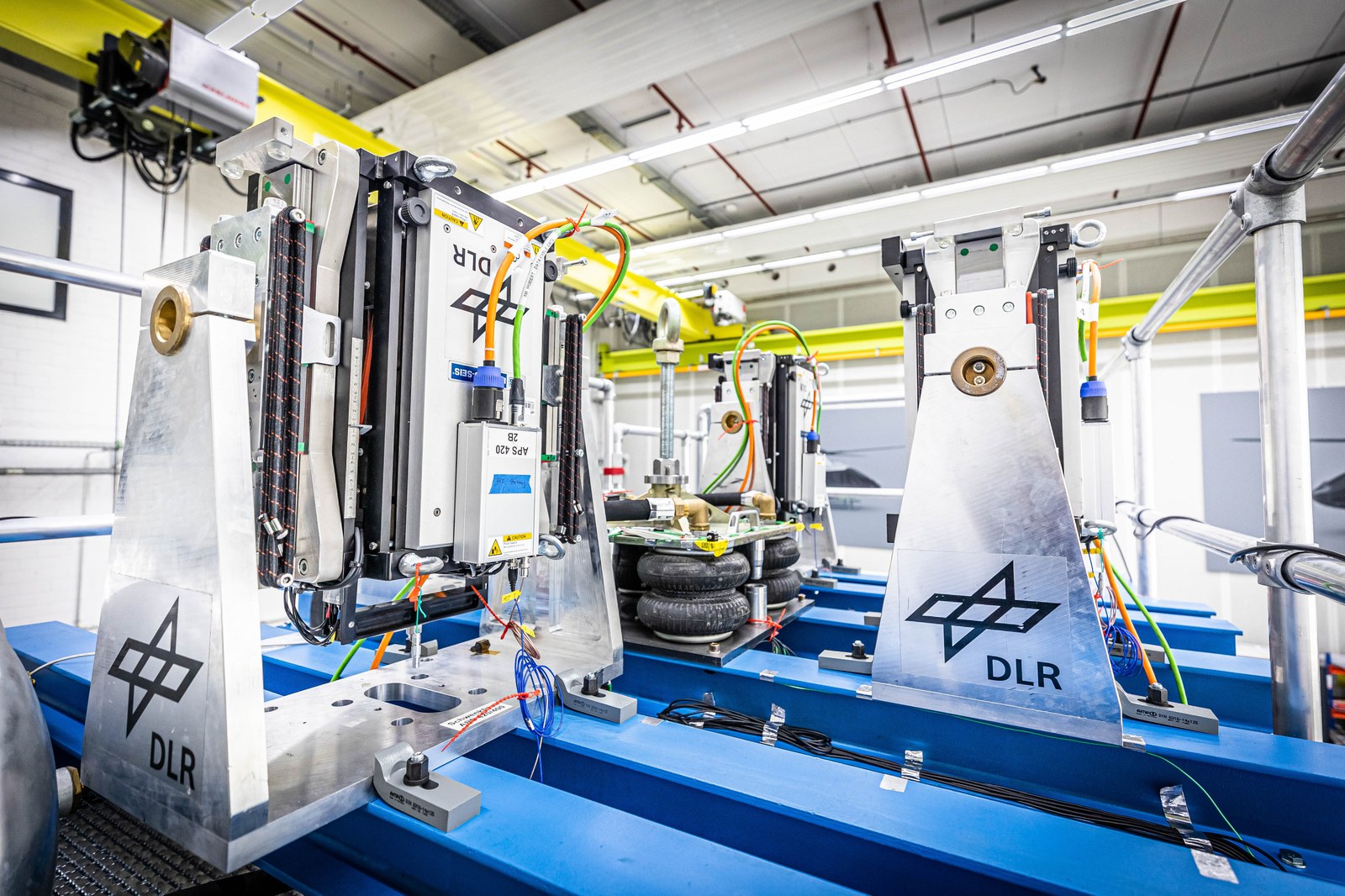
Airbus Helicopters
Zukünftige Hubschrauber verbessern
Flugverhalten, Strukturbelastungen, Vibrationen, Passagierkomfort, aber auch der Lärm eines Hubschraubers werden durch die sogenannte Aeromechanik bestimmt. Während Aerodynamik das Verhalten in Bezug auf die Luftkräfte, wie Auftrieb und Widerstand, beschreibt, bezeichnet Aeromechanik das Zusammenspiel von Aerodynamik, Flugmechanik und Strukturdynamik. Sie spielt bei der Entwicklung neuer Hubschrauberkonzepte eine wichtige Rolle. Das Projekt eVolve hat zumZiel, die Vorhersage der Aeromechanik zu verbessern. Das reduziert das Entwicklungsrisiko und die Zeit bis zur Markteinführung, sowohl bei klassischen Hubschraubern als auch bei neuartigen Drehflüglerkonzepten wie Lufttaxis. Unter der Leitung von Airbus Helicopters Deutschland forscht das DLR zusammen mit Airbus Defence & Space, der Universität Stuttgart sowie der Technischen Universität München in dem Projekt. Die DLR-Wissenschaftlerinnen und -Wissenschaftler entwickeln in eVolve unter anderem Simulationsmethoden, mit denen die Aeromechanik von Hubschrauberrotoren besser modelliert werden kann, sie erstellen eine Datenbank, die die Schallabstrahlung von Lufttaxis vorhersagt, und sie entwickeln Ansätze zur Vorhersage und Dämpfung von Vibrationen. Seitens des DLR sind die Institute für Aerodynamik und Strömungstechnik, für Aeroelastik, für Flugsystemtechnik sowie das Institut für Softwaretechnologie beteiligt. Das Projekt ist im September 2021 gestartet und endet im August 2024.

Ein Beitrag von Johannes Knebusch und Marc Böswald aus dem DLRmagazin 174