TRIPLE-IceCraft expedition to Antarctica – final system tests and completion of preparations for drilling – part 4
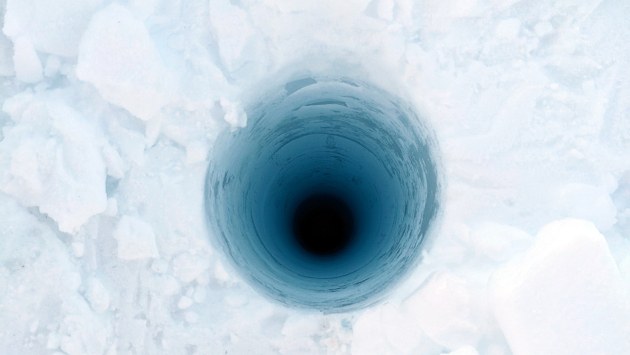
Soon it will be time for the big test of our TRIPLE-IceCraft probe, which is to melt its way through the almost 100-metre-thick ice shelf north of Neumayer Station III. But before that, we still have to perform final system checks and make a first test borehole.
The camera system and the Forefield Reconnaissance System (FRS) are now installed, but we are now facing a challenge. Inside the probe, all subsystems are connected to each other via a data bus for communication. Since the beginning of the tests, communication interruptions between the systems in the front module and the systems in the rear module have occurred repeatedly. We checked all of the connectors and cables in the front module during the installation of the camera module but did not find any faults. And so we must now open the rear module as well. To do this, we first have to close the front module again.
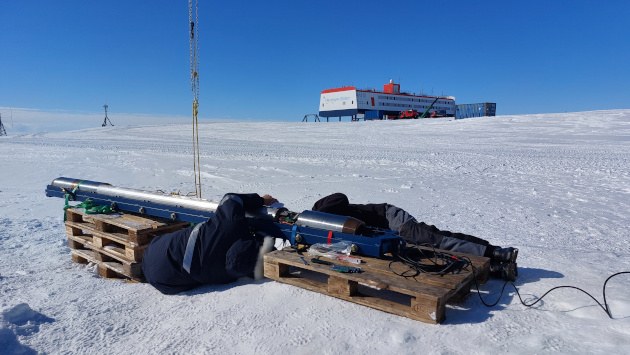
An initial inspection shows no apparent faults or damage here. We check every connector and every cable. This takes a lot of time because the electronics are highly integrated and arranged to best use the limited space inside the probe. In order to inspect all components, others must first be removed. However, after a tedious search, we finally found the fault – a defective soldered connection on a power supply module for the communications system. Two soldered contacts between the board and a connector are broken, probably as a result of damage during transport. The solution is clear – we remove the module and replace the connector and the soldered connection. In addition, we fix the socket to the board and attach another strain relief to the cable. A short test and finally the communications in the probe work stably again. Now everything is reassembled, and the rear module is closed.
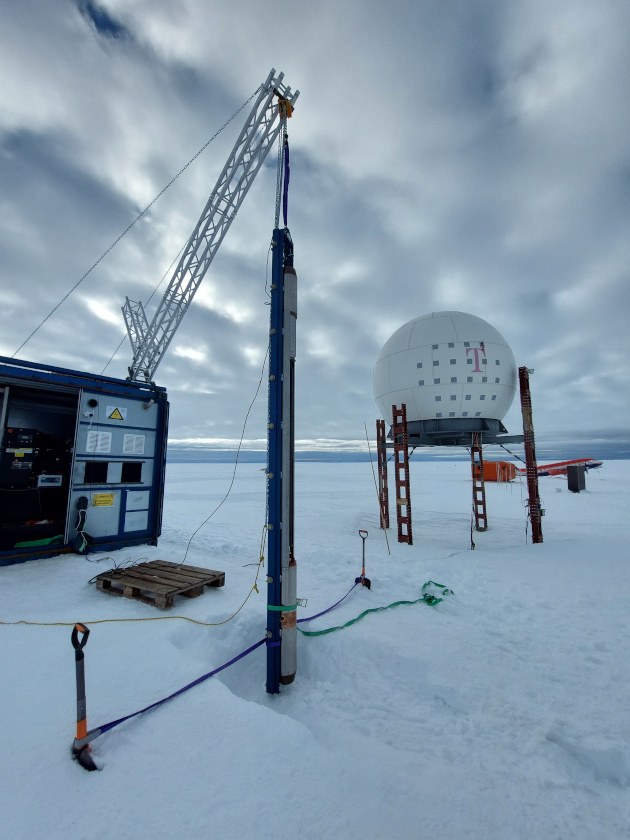
Next, we recalibrate the force sensors, as the new systems have changed the weight of the probe. To do this, the probe is first calibrated to zero while lying down and then suspended from the crane and calibrated with the force of its weight. Unfortunately, the bad weather forces us to take another break of one and a half days. The wind speeds reach over 40 knots (approximately 74 kilometres per hour), the outside temperature is minus 10 degrees Celsius, and the snow is drifting very heavily. Visibility is severely limited as a result, and working outside the station is not possible. The cold wind and snow sting the skin even when walking short distances.
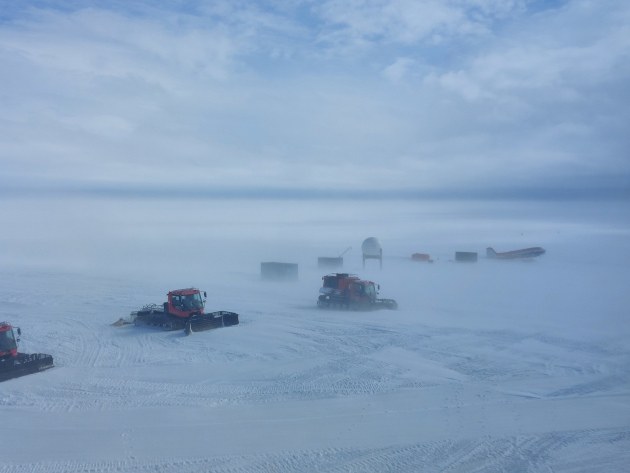

When the weather improves again, we are able to perform final tests of the heating and winch systems. To do this, we need to melt down to a depth equal to the length of the entire probe and then retrieve it. First, we start with the drilling procedure – the probe is initiated and manually lifted onto the crane. All sensor values and subsystem statuses are checked. Everything works, and the test can begin. The launching device pulls the probe up about 10 centimetres on the crane. To start, the winch system is sent the command to move downwards. It takes a short moment; then, we hear the motors start up and the gears turn. The probe begins to move and travels steadily towards the ice at a speed of about seven metres per hour. When it reaches the ice, the cold, previously unheated melting head touches down. The probe’s internal force sensor and control system detects the touchdown, and the probe reduces its speed until it stops. We stop the probe by command and initiate the upward movement. Again, we have to wait a bit to hear the restart. The probe starts moving again and travels upwards at the same speed. After a few centimetres, an unexpected event occurs; the probe stops, moves downwards towards the ice again and is slowed down by hitting the ice. The cable has slipped through the drive wheel. How did this happen? This never occured during the pre-tests.
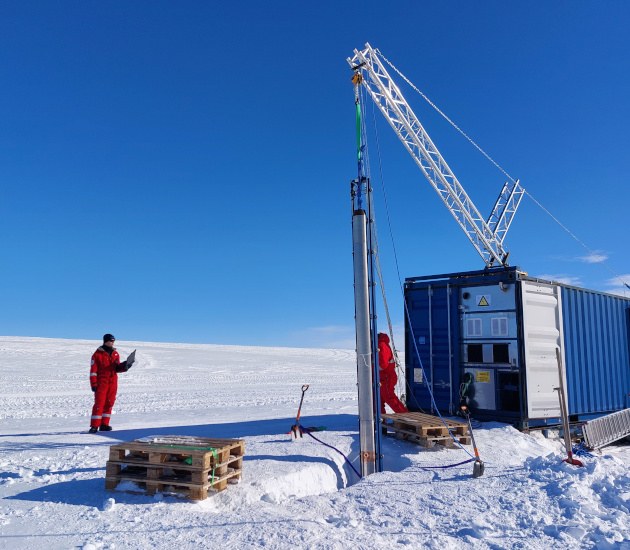
During the following days, we work on solving the problem. We inspect the cable and the drive wheel, but can't find any dirt or damage. We revise the coiling system and investigate possible differences compared to the previous tests. These were conducted in warmer environments. Therefore, we heat the probe in the area of the coiling system and try again. The cable slips again. We recalibrate the force sensors and optimise the control of the coiling system. We increase the pre-tension on the drive wheel and rework the cable routing. In the meantime, the cable sits more firmly in the drive wheel, but it still slips through again. The problem seems to be too little friction between the cable and the drive wheel. We are sure we can correct this by reworking the drive wheel, but the necessary machines are not available at Neumayer Station III.
In order to still be able to carry out the drilling, we decide to support the probe externally during its return journey. To do this, we use a rope, one end of which we attach to the rear of the probe and the other to a winch. The rope is guided by pulleys so that it is as close as possible to the cable, and both can be guided side by side. By manually operating the winch, we can now relieve the load on the internal winch system. The relief control can be done by measuring the force in the internal winch system. This measurement determines the force with which the probe hangs on the melting probe cable. By readjusting the external winch, we can divide the weight force equally between the melting probe cable and the retrieval rope. With this support, driving in reverse and reeling in the cable finally works.
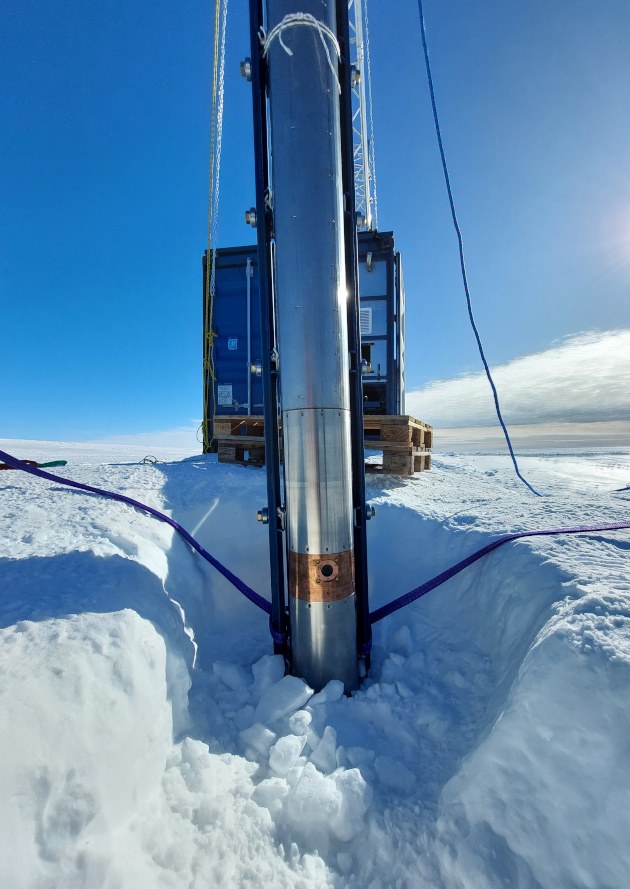
Next, we test the probe's heating system. We start with about one kilowatt of heating power at the front melting head. The TRIPLE-IceCraft melts evenly into the ice at a constant speed. The outer sides of the probe are regulated to a temperature a few degrees above zero Celsius, just enough to prevent the probe from freezing to the side of the ice channel. As long as the melting probe is still in the air, the supply cable must limit the electrical current, otherwise the coiled cable inside the probe will quickly overheat. We use the TRIPLE-IceCraft to melt down approximately one metre and then stop the melting process. Then we drive up with the support of the external cable. After TRIPLE-IceCraft arrives back on the launch device, we stop the journey. Then we repeat the melting process and drive the probe approximately four metres into the ice, corresponding to the probe's length. During the melting process, we photograph the ice in the melting channel and do not detect any obstacles or other anomalies in front of the probe through the FRS. We then begin the return journey and recover the TRIPLE-IceCraft.

We stow the equipment and prepare the drilling system on the north pier. Finally, it's time to transport everything to the drilling site.
Tags: