Factory of the Future
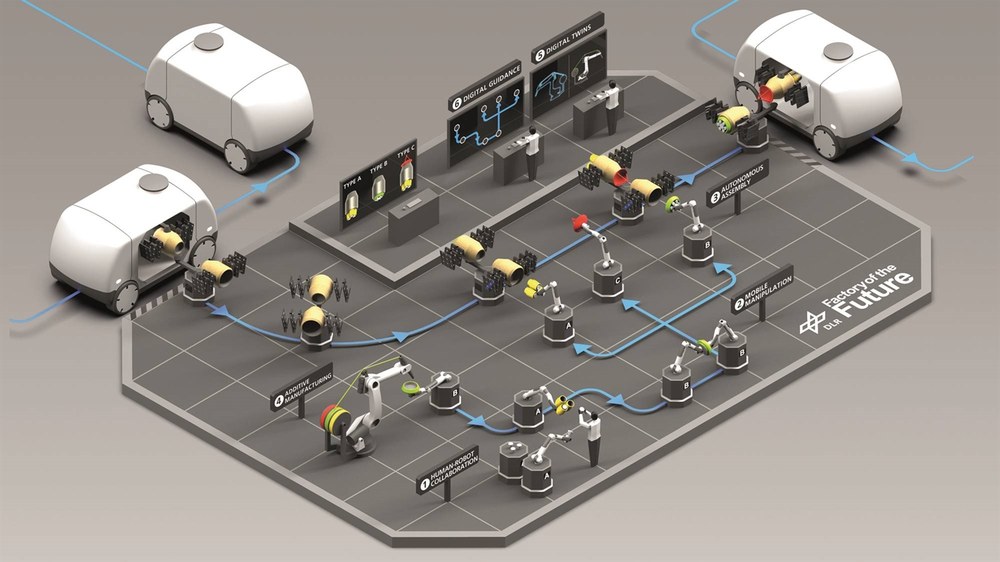
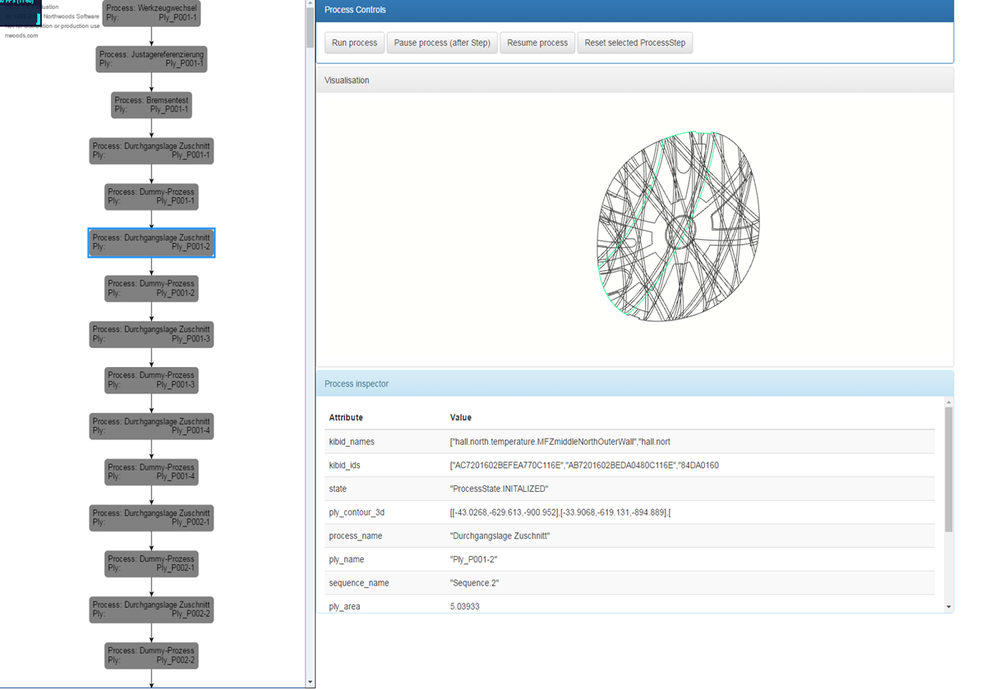
Duration: 2017-2021
The Factory of the Future Project is a DLR-wide project, in which a total of ten institutes are involved. The main goal is to meet the challenges in the context of demographic change, globalisation and digitalisation. In order to continue to be successful in international economic competition, it is essential to combine strengths in automation, mechanical engineering, electrical engineering and material and process engineering with new digital technologies. A central question in this context is that of the future of work against the background of demographic change. Can the digitalisation of production compensate for the shortage of skilled workers and how should machines be designed so that they are perceived as an optimal aid and not as a threat? In production, on the other hand, the trend today is increasingly towards individualised (customer-tailored) products, with exploding variant diversity and ever shorter product cycles.
Overall, there are three main streams in this project:
- Development of new digital production chains from digital model to automatically assembled product. In doing so, resource and energy consumption as well as costs are reduced and human personnel are relieved despite flexibilisation.
- Establishment of versatile digital production concepts through mobile robotic systems and networked, intelligent production and assembly robots.
- Safe, highly efficient and intuitive cooperation between humans and robots and between humans and machines in general in the cognitive production system of the future.
The aim of the synergy topic Factory of the Future is to develop a wide range of digital production technologies, robot systems and applications for flexible and networked manufacturing processes and to demonstrate them in two to three lead scenarios. One focus is on the realization of robust robot-supported manufacturing processes using digitalisation approaches and Industry 4.0. The aim is to make aerospace applications in particular more efficient, cost-effective, safe and resource-saving, from the factory on the ground to operations in space and in the air. From pilot projects in these DLR-specific areas, the approaches should find broad industrial application through targeted technology transfer. DLR's robotics development, which is driven by space travel, and the use of cooperating robots in the production of aerospace components have a pioneering function throughout Europe and have a significant impact on other sectors of industry. Major trends and standards in modern robotics are set by DLR.
The following topics are currently being worked on:
- Intelligent process control system: This system is able to coordinate the individual stations during production, assign tasks to them and thus control the entire process flow. This is largely automated, i.e. the system can control the production process from a given construction plan alone. This system is to be iteratively further developed in the coming years in order to be prepared for the future challenges in the area of Industry 4.0. The latest developments in the field of industrial control technology will be integrated - examples are the integration of Publisher/Subscribe technologies, TSN (Time Synchronous Networks) and Safety over OPC-UA. All calculations are also visually displayed and made available to the user. On a more abstract level, the correctness of the considered control programmes also plays a role here.
- Offline programming systems: Based on a tool for handling semi-finished products such as carbon fibre mats, the ZLP is working on automatic gripping and depositing planning for pick-and-place applications. This starting point is the two- and three-dimensional constructions in a CAD system as well as the available grippers. The system uses this information to calculate the gripping and dropping points of the respective fabrics. Often a blank has to be handled with more than one gripper and more than one , which makes collision-free path planning for several collaborating robots necessary. These two systems are also integrated into the process control system described above so that it can make use of their capabilities. The offline programming system also showed its flexibility when it could also be used in other areas of application such as the handling of aluminium sheets. A further component is a camera-based system that can recognise carbon fibre fabrics and thus enable targeted gripping, regardless of the position of the blank, for a pick-and-place process.
- Augmented/Virtual Reality in aviation production: One of the main applications of AR or VR in production technology is the interaction between man and machine. Preliminary tests have already been carried out here, in which it was shown that it is possible to locate a worker in 6D coordinates from four localisation stations using an Ultra Wide Band tag. Interactions with and remote control of the robot are already possible by means of speech recognition, whereby the robot is visualised by a HoloLens. Furthermore, projections of virtual quality assurance data onto the real component are possible in the HoloLens in order to compare measurement data and reality.
All the techniques developed were presented to a broad specialist audience at the Augsburg Production Technology Colloquium in May 2019 as part of the ZLP's ten-year anniversary.

Video: IROS 2018 Fan Challenge
Your consent to the storage of data ('cookies') is required for the playback of this video on Youtube.com. You can view and change your current data storage settings at any time under privacy.
Publications
- Algebraic Derivation of Until Rules and Application to Timer Verification
- Distances, Norms and Error Propagation in Idempotent Semirings
- Smart Manufacturing of Thermoplastic CFRP Skins
- Path Planning of Cooperating Industrial Robots Using Evolutionary Algorithms
- IROS 2018 Fan Challenge - Team DLR Augsburg