Rotorcraft Department
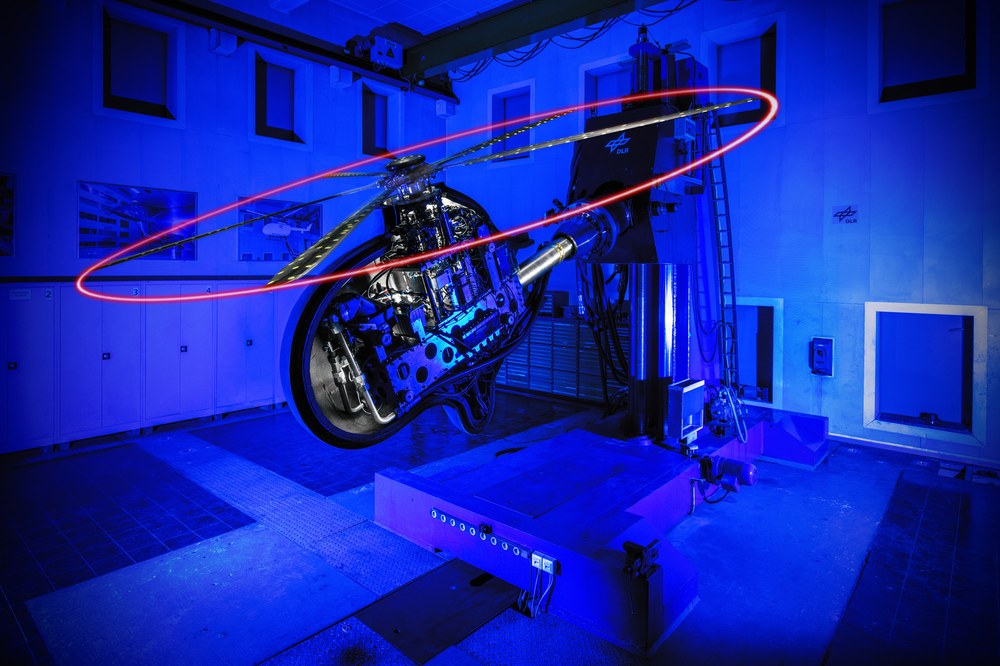
The Department Rotorcraft at the DLR Institute of Flight Systems focuses on rotor system and flight system technology for helicopters and other rotorcraft configurations. The goal of these activities is to support the development of new technologies and evaluate them in terms of improving flying characteristics, handling qualities, safety, economic efficiency, environmental compatibility, and mission effectiveness. The department's work includes system analysis, modeling and simulation of rotorcraft configurations and system components, as well as wind tunnel tests and in-flight testing.
As a fundamental prerequisite for the design, development and evaluation of innovative rotorcraft technology, comprehensive rotor dynamics and flight dynamics simulation models are available. These configurable models are validated by comparison with flight test and wind tunnel data.
For stability analyses and flight control law design , system identification methods and parameter optimisation are used. The integrated overall systems are analysed, optimised and evaluated with the help of flying and handling qualities methods and metrices. This approach has resulted in the ability to define and specify flying and handling qualities criteria for existing and future rotorcraft.
Working-Groups

