HEX 4 ELECTRA
Why is waste heat a challenge?

And if it gets too warm?
If the optimum operating temperatures of the components are exceeded, the performance, durability and safety of the components may be jeopardised. This can result in limited functionality or even complete failure of the components.
In fuel cell-based aircraft engines, the thermal management system can account for a large portion of the weight and volume of the entire propulsion system. The aim of the research is to increase the power density of the overall propulsion system by developing lightweight, compact heat exchangers.
Triply Periodic Minimal Surfaces (TPMS)
At the Institute of Electrified Aero Engines, we are researching 3D-printed models ofa TPMS (Triply Periodic Minimal Surfaces) cooling structure, which consists of periodically shaped geometries with a very high surface-to-volume ratio.
An additive manufacturing process is well suited to producing such complicated shapes. The fine structure of the object is not a new development by the scientists, but - like many other technical developments - was inspired by nature and can be found, for example, in the wings of insects.
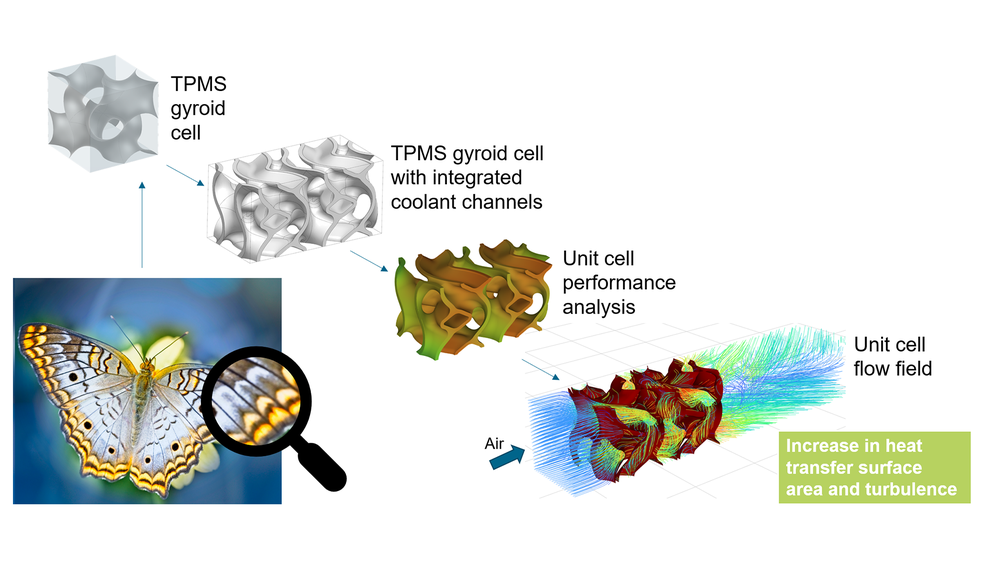
Innovative coolant routing
The institute is researching various TPMS geometries with integrated cooling channels. These models are used to experimentally validate complicated and complex calculations on the basis of real component tests. This determines the optimum aerodynamic and thermal performance of the heat exchangers and thus verifies the success of the design.

These types of tests are currently being carried out at the Institute in the Fluid Centre at BTU Cottbus-Senftenberg and are planned for the future on a larger scale in the HepCo (Hybrid Electric Propulsion Cottbus) test environment in Cottbus.
The development of compact heat exchangers has reached Technology Readiness Level (TRL) 4 at the Institute of Electrified Aero Engines by validating the concepts under laboratory conditions.
