Resistance welding
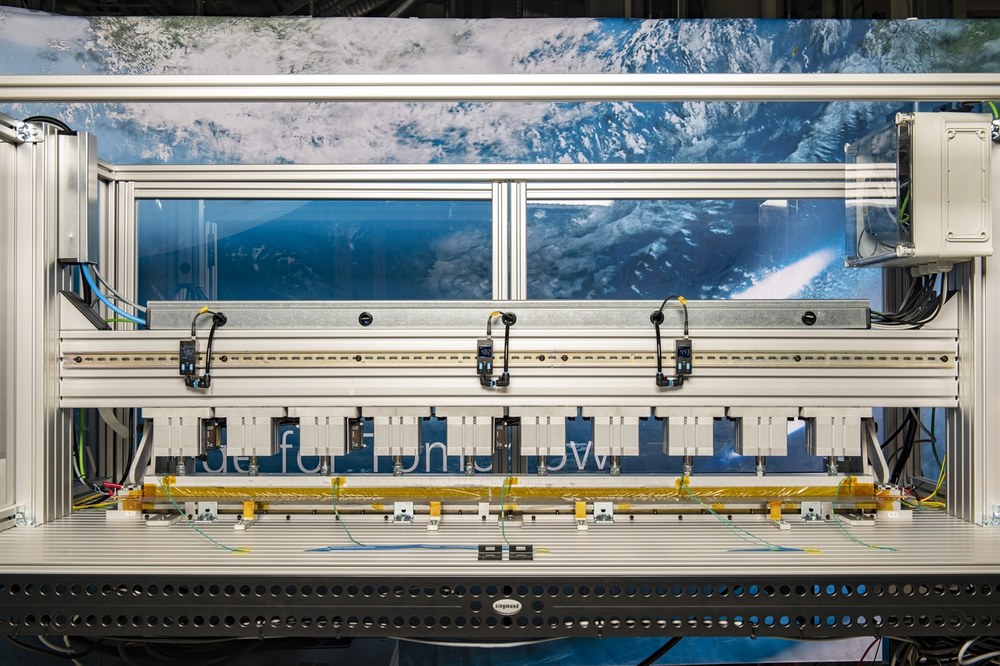
DLR
Functional principle
Resistance welding itself is known as a comparatively simple and efficient joining technique. An electrically conductive welding element made of carbon fibre is inserted into the joining zone, to which a voltage is applied along its length. The current flow leads to Joule heating, which melts the welding element and the surfaces of the neighbouring parts. The simultaneous application of pressure achieves a very good connection between the components.
Test rigs
DLR Augsburg has test rigs of various sizes for the further development of the process. For example, smaller components such as clips with robot end-effectors or large components with weld seams of up to 1500 mm can be welded with a static system. DLR Augsburg is a world leader in the use of carbon fibre welding elements, which guarantee the purity of the assembled component.
All welding stands are also equipped with extensive sensor technology to reliably control the process and use the data for quality assurance.
Application examples
Welding thermoplastic fibre composite components offers the possibility of changing assembly sequences, e.g. in aircraft production. In the metal sector, aircraft systems are currently only integrated after the structure has been assembled, as these can be damaged by chips from the riveting process. However, this sequence has the disadvantage that limited accessibility makes assembly considerably more difficult.
In addition to use in the aerospace industry, there are other areas of application for resistance welding in the field of thermoplastic components, e.g. in mechanical engineering, electrical engineering, the automotive industry, boat building, medical technology and conveyor technology.