STORT flight experiment - Key technologies for high-speed return flights of launcher stages
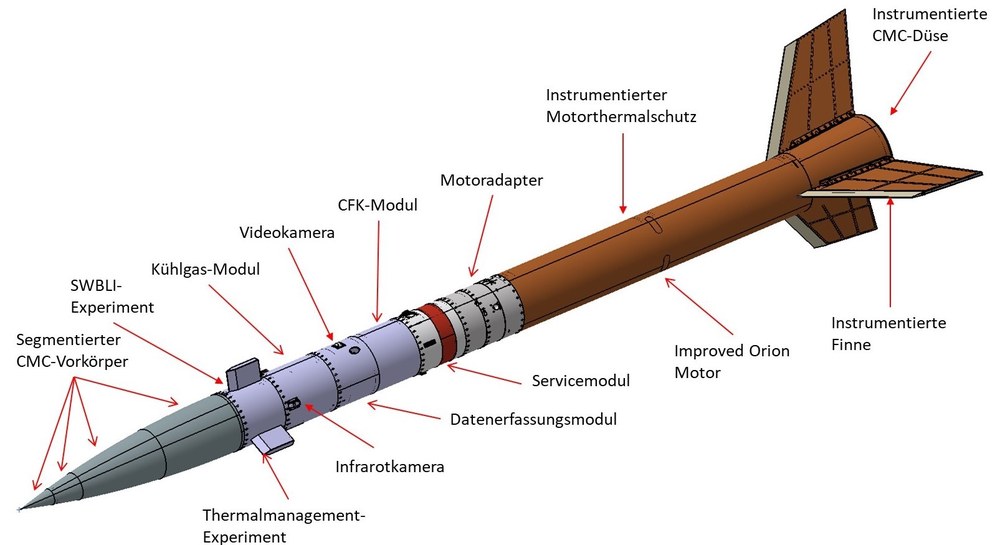
High standards for space transportation systems in particular concerning their reliability put tough requirements on design and analysis tools. Simulation tools used for this application need to be improved and validated by means of reliable experimental data in order to reduce uncertainties in prediction of flight loads and spacecraft response. In spite of significant progress in development of numerical methods there is a significant gap in multidisciplinary simulation of complete space transportation systems. The improvement of test facilities and fight experiments by means of advanced and reliable measurement techniques is one of the key elements to provide the needed experimental data. Cost reduction in space transportation is another essential element for the establishment of a competitive European space industry. Reusability of launcher stages is thereby one of the promising elements for cost reduction.
The forebody of the vehicle consists of high temperature CMC panels which are extensively instrumented with heat flux sensors, thermocouples and pressure sensors along four longitudinal lines every 90° in circumferential direction. Three fixed canards with a CMC outer shell are used to qualify thermal management concepts. While an impingement cooling will be integrated in the first canard, the second canard is passively cooled. The third (reference) canard without any cooling will serve to perform a Shock Wave Boundary Layer Interaction (SWBLI) experiment, which requires dedicated instrumentation with fast response time to measure the foot print of the SWBLI around the canard. For the first time a miniaturized IR-camera will measure the canard outer surface temperature in hypersonic flight. Two additional video cameras will monitor the fins of the third stage.
For sounding rocket flight experiments the structure is normally metallic e.g. Aluminum alloy. Motivated by mass reduction potential, a hybrid module made of CFRP and metallic structure was developed and qualified during the ATEK flight experiment. Within the STORT project a lightweight pure CFRP module with integrated Fibre Bragg Grating (FBG) sensors will be developed and flight qualified. The motor case is also instrumented with FBG sensors to measure the temperature distribution along the surface exposed to the supersonic / hypersonic flow. One of the upper stage fins is instrumented with different types of sensors. Strain gauges and thermocouples are implemented at several locations of the fin structure. Pressure sensors on both side surfaces should allow to measure the pressure difference depending on the flight profile. The tailcan instrumentation consists of strain gauges, thermocouples and pressure gauges. A CMC nozzle with significantly lower mass compared to the standard nozzle made of graphite and ablative materials is under development and will be ready for the flight after passing extensive thermo-mechanical tests, static firing test and a one-stage flight experiment.
Recent studies show that reusability becomes feasible if the separation of the reusable first stage takes place at Mach numbers between 8 and 12. Previous hypersonic flight experiments like SHEFEX-II achieved Mach numbers up to 10 for a hypersonic flight time of approx. 30 seconds and therefore provided only limited integral thermal loads. The coming flight experiments ReFEx and CALLISTO have their main focus on guidance and navigation at lower Mach numbers and landing and do not achieve high aerothermal loads on the vehicle structure. To close this gap and achieve high integral thermal loads on the vehicle the flight experiment STORT (Key Technologies for High-Speed Return Flights of Launcher Stages) will fly at hot hypersonic flight conditions for a longer time using a three-stage sounding rocket configuration. The third stage will fly a suppressed trajectory at Mach numbers above 8 in an altitude range of 45 km to 55 km with a duration of approx. 120 seconds to generate high integral heat loads on the structure.
Project | STORT |
---|---|
Term | 1/2019 - 12/2022 |
Client | The project is being carried out as part of the institutional funding provided by the Space Research and Technology program. |
Partners |
|