Aeroelastic Design
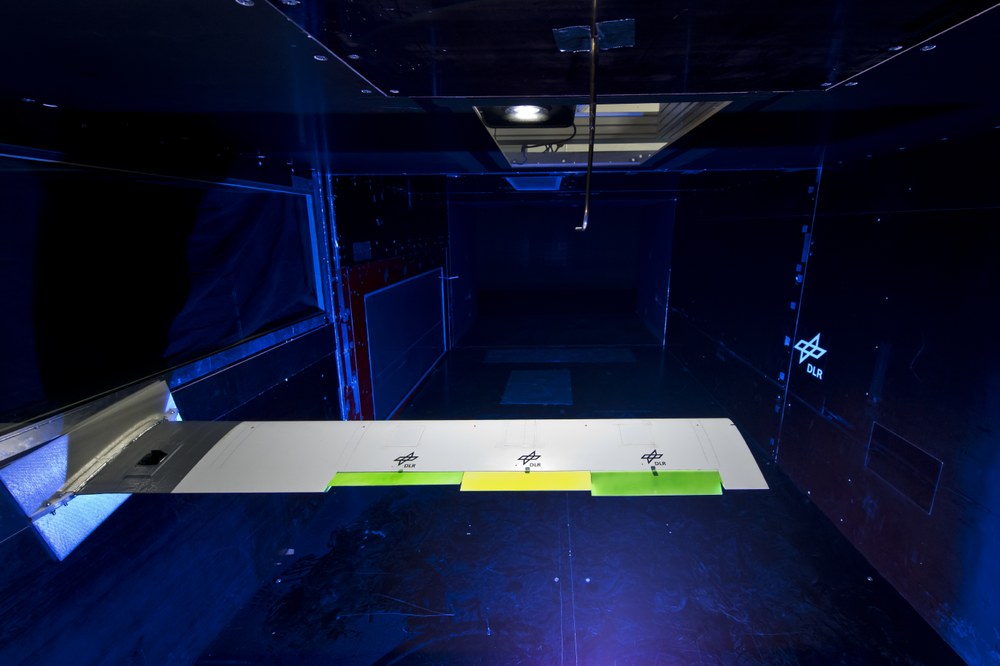
In the research topic of aeroelastic design, we deal with various design tasks in the context of the aeroelastic design of an aircraft, an aircraft component or a wind tunnel model. The development of methods ranges from conceptual design and preliminary design to detailed design for manufacturing, in particular for wind tunnel models.
The focus of the design is on the structure and the aeroelastic properties (aeroelastic loads, control surface effectiveness, flutter and divergence). The parametric structure of the simulation models for the design and the use of fibre composite materials (keyword "aeroelastic tailoring") are of particular importance. The combination of parametric modelling, structural design and load analysis leads to a parametric design process, which was also developed in the group and is continuously being further developed. The existing methods are also suitable for the structural design of rotor blades for wind turbines.
Parametric modelling
The aim of parametric modelling is to set up all simulation models involved in the design process using typical parameters from aircraft design (e.g. profile coordinates, wing planform parameters) or typical parameters from structural design (parameters for describing the design of a load-carrying component, e.g. spar and rib positions for wing box structures). In addition to the geometric and structural parameters, the parameterisation also includes specific parameters for the structural modelling as a finite element model (e.g. mesh refinement), the aerodynamic modelling, the coupling models between aerodynamics and structure and the structural optimisation model. The latter includes the parametric definition of design variables (e.g. wall thicknesses of a defined design field) and the definition of boundary conditions (e.g. permissible stresses and/or strains). The software for parametric modelling is the ModGen computer program developed at AE-LAE.
MONA design process concept
The concept of parametric modelling with ModGen enables the uniform generation of simulation models for load analysis, structural optimisation and aeroelastic analysis for the entire aircraft or for components for MSC Nastran. The set-up of an individual aeroelastic design process (e.g. in a shell script), depending on the task, consisting of parametric modelling with ModGen and the use of MSC Nastran for load analysis, aeroelastic analysis and structural optimisation is referred to as MONA.

Parametric design process cpacs-MONA
The parametric design process cpacs-MONA for the complete aircraft combines the concept of parametric modelling, load analysis and structural optimisation in one integral process. On the other hand, the interface to the CPACS data format enables the use of aircraft configuration data in a DLR-wide standardised form. MONA stands for the design process concept of the same name, consisting of the parametric model generator ModGen and the comprehensive structural analysis programme MSC Nastran. The latter is used for the load analysis of the flexible aircraft as well as for component-by-component structural optimisation and aeroelastic analysis (e.g. flutter analysis). Prior to the MONA design process consisting of parametric modelling, load analysis and structural optimisation are upstream calculation modules for determining initial loads prior to structural design and for creating an initial mass model for the aircraft configuration, including various mass models for loading and refuelling scenarios. Interfaces to externally calculated loads or the take-over of structural parameters of external finite element models are avaiable as well. Git-based version control systems are used to ensure sustainable software development of cpacs-MONA.

Aeroelastic Tailoring
The use of fibre composite materials in the structural design of aircraft wings offers additional possibilities for designing the structure with regard to aeroelastic requirements (e.g. passive load alleviation, control surface effectiveness, flutter). In particular, the concept of using so-called lamination parameters as design variables in conjunction with gradient-based structural optimisation methods is being used and further developed. The flight loads required for dimensioning are calculated as part of the aeroelastic tailoring process tAElor in the design group within structural optimisation, so that the influence of the loads resulting from the structural design can be taken into account directly in the structural optimisation.

Structural design of wind tunnel models
Parametric modelling methods (ModGen) are used for the structural design of wind tunnel models to investigate aeroelastic properties. When using fibre-reinforced composites, it is thus possible to map the detailed design, such as the detailed layer set-up, in a suitable structural model using a finite element model in an early design phase and to carry out corresponding aeroelastic analyses.

Concept design methods
Even before the availability of simulation models (aerodynamics and structure) for calculating aircraft loads (flight and landing loads), methods were developed to determine initial loads for an aircraft using analytical procedures. These are available as independent modules in DLR-wide design chains with a CPACS interface and are also implemented in the parametric design process cpacs-MONA.