Rocket engine technology
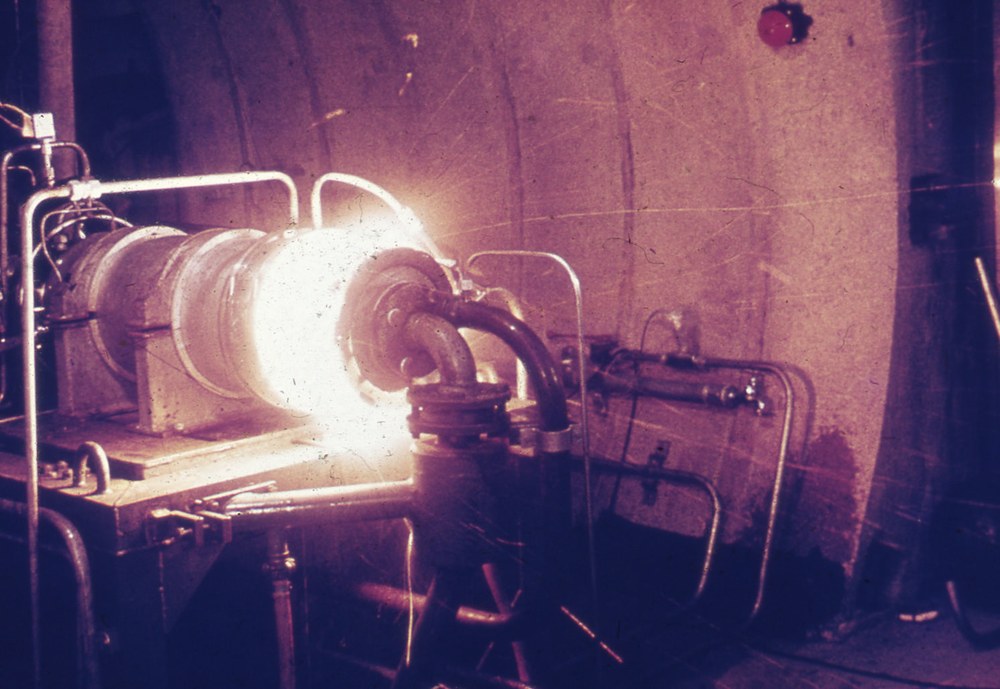
For a launch vehicle to take off, it needs thrust. A rocket engine generates thrust by ejecting hot combustion gases very quickly through the nozzle (conservation of momentum). Chemical propulsion systems can be categorized into liquid, solid and hybrid propulsion systems. In liquid propulsion systems, both the oxidiser and the fuel are stored in a liquid phase (e.g. liquid oxygen and liquid hydrogen). The oxidiser and fuel are injected into a combustion chamber and ignited there. Liquid propulsion systems are characterised by their high thrust efficiency but the propellants are hardly storable. In solid propellants, the oxidiser and fuel are already premixed in a solid phase (similar to a New Year's Eve rocket) and only need to be ignited. As a result, their design is simple and they have a high thrust. This is why they are popular for tactical applications. However, the thrust of a solid propellant engine cannot be changed (or only with great difficulty). Hybrid propulsion systems, in which the oxidiser is stored in liquid form and the cylindrical fuel block (plastic, butadiene/rubber or wax) in solid form, can be categorzied inbetween solid and liquid propulsion systems. Hybrid drives are relatively simple, yet flexible, controllable and can be ignited multiple times.
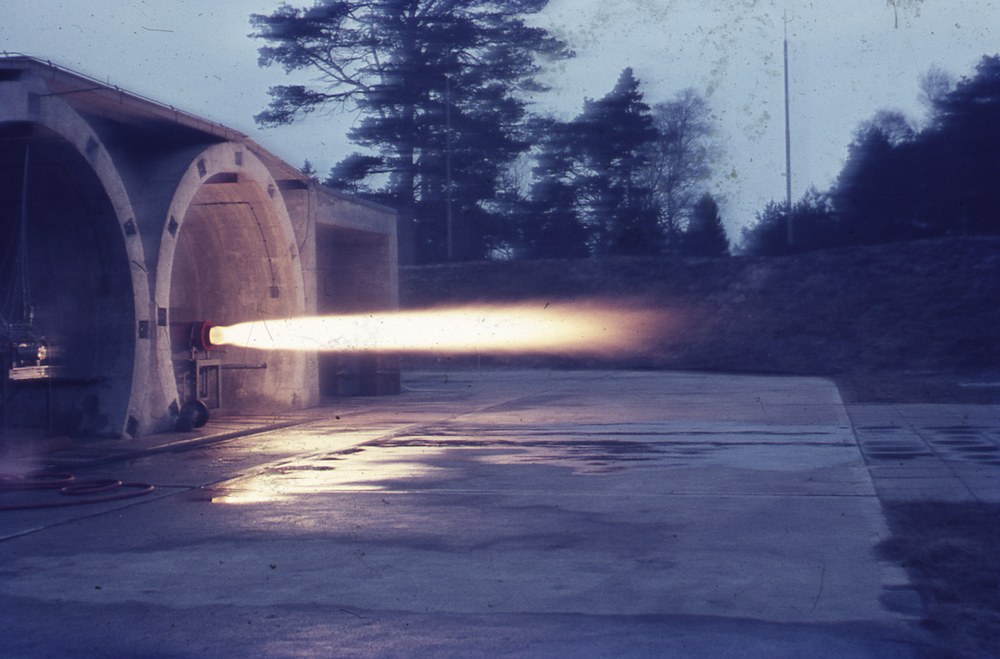
In the context of "Responsive Space", the Launch Segment department is researching solid and hybrid propulsion systems (ATHEAt). Solid and hybrid propulsion systems are the key technologies for responsive launch systems, as solid propulsion systems in particular can be stored and are quickly ready for use. Hybrid propulsion systems, on the other hand, can use storable oxidisers, but must be refuelled before use. However, thanks to their controllable thrust, they offer the unique possibility of precisely placing critical payloads in the desired orbit and reacting to unexpected deviations. Possible combinations of both technologies include the use of multiple-stage launch systems consisting of solid propulsion in the main stages and hybrid propulsion in the upper stage. The Launch Segment department is investigating possible applications, including development and engine testing.
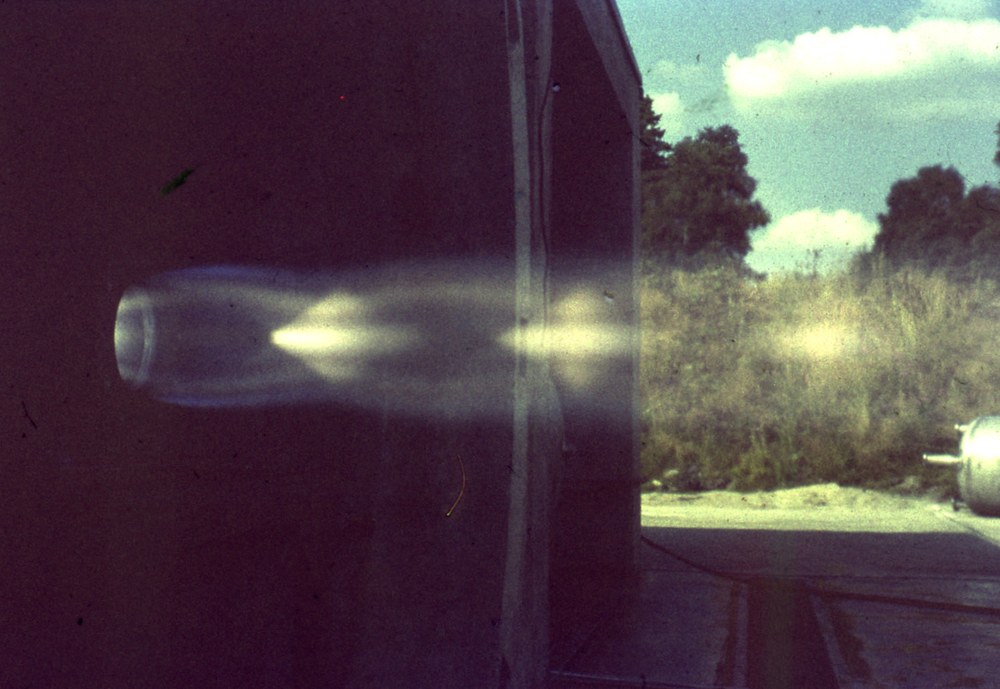
An infrastructure is being created at the Trauen site, ranging from propellant production (Technical Center) and mobile refuelling solutions (MoHyPer) to test facilities that are unique in Germany. The defined goal is to test one tonne of solid fuel mass and burn it off in a controlled manner. By understanding and controlling the necessary steps (development, production and burn-off tests), the launch segment is positioning itself as the ideal contact and problem solver for engine technologies that enable responsive satellite deployment. This allows the necessary shareholders in Europe to be brought together. There are also opportunities for cross-institute co-operation and sharing of the test infrastructure.