Effiziente Technologien für die Rumpfstruktur - Airbus
Wie lassen sich die eigenen Produkte optimieren, damit der Nutzen für den Kunden steigt? Eine solche Frage stellt sich sicher jedes Unternehmen. In der Luftfahrt ist dabei eine Antwort beinahe omnipräsent: Man müsse das Gewicht der Bauteile reduzieren. Und wenn das noch mit einem kostengünstigeren Herstellungsprozess einhergeht, hätte man gleich doppelt gewonnen. Genau das hat sich Airbus auf die Fahnen geschrieben.
„Schon vor Jahren hatten wir bei Airbus die Vision, einen neuen Stand der Technik für Rumpfbauteile zu schaffen“, sagt Anna Bauch, die das R&T Development and Partnerships Germany bei Airbus leitet. „Dabei haben wir einerseits an neuen CFK-Technologien geforscht und andererseits 3-D-gedruckte Komponenten aus Metall in unsere Flugzeuge eingeführt.“ Nun haben CFK, also kohlefaserverstärkte Kunststoffe, und 3-D-Druck von Metallen auf den ersten Blick nicht viel gemein. Doch beide wären geradezu prädestiniert, wenn man neuartige Technologien für gewichtsoptimierte Rumpfstrukturen suchen wolle, meint die Ingenieurin.
Weniger komplexe Bauteile sparen Gewicht und Kosten.
In LuFo V-1 rief der Luftfahrtriese aus Hamburg deshalb IMPULS-Rasant ins Leben. Beim Verbundprojekt IMPULS waren die Partner auf der Suche nach innovativen, mittelfristig implementierbaren und kostensparenden Lösungen für CFK-Rumpfstrukturbauteile. RASANT war ein Teil davon und steht für „Rumpfbauteile basierend auf neuen Technologien“. Hier hatte sich Airbus die Spanten vorgenommen. Diese bilden das Grundgerüst des Flugzeugs. Sie geben Stabilität und „tragen die Haut“, die über Clips daran befestigt ist. Besonderes Interesse galt dabei den Türrahmenspanten. Das liegt daran, dass im Bereich der Türen hohe Lasten auftreten, was sich wiederum in den Fertigungsprozessen niederschlägt.
„Bisher wurden die Spante und die Clips differenziell hergestellt“, sagt Anna Bauch. Das heißt, dass viele Komponenten an den vorgefertigten Spant angebracht werden mussten. Bei diesem fertigungslastigen Prozess entstand ein komplexes Bauteil. „Bei IMPULS-Rasant hat das Projektteam nun einen CFK-Integralspant entwickelt“, erklärt sie weiter. Die Clips sind da schon dran. „Nun haben wir viel weniger Bauteile, was nicht nur die Komplexität reduziert, sondern auch an Gewicht spart. Zusammen führt das wiederum zu einem deutlichen Kostenvorteil.“
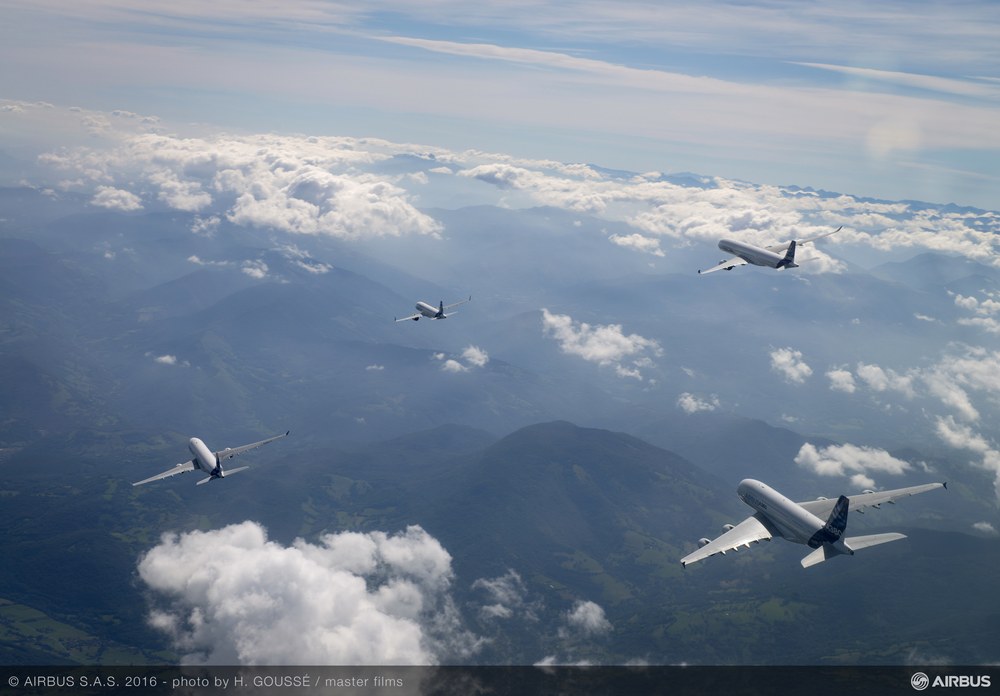
Airbus S.A.S.
Dass unser Prozess den hohen Anforderungen der Luftfahrt gerecht wird, haben wir reproduzierbar bewiesen.
Nicht Kohlefasern, sondern Metallstrukturen standen im Mittelpunkt eines weiteren LuFo-Projekts, mit dem Airbus und Premium Aerotec die Rumpfstrukturtechnologien optimieren wollten – ALM2AIR. ALM steht dabei für Additive Layer Manufacturing, umgangssprachlich auch 3-D-Druck genannt. Im Projekt hatten sich die Teams das Pulverbettverfahren vorgenommen. Bei diesem fährt ein energiereicher Strahl über ein Bett aus pulverförmigem Metall. An den Stellen, die später zur Wandung werden sollen, schmilzt das Metall. Sobald es erstarrt, bildet es eine Lage des Bauteils. Das Bett wird geringfügig abgesenkt und der Prozess beginnt von vorn. Schicht für Schicht wird nun das Werkstück aufgebaut. Auf diese Weise sind selbst komplizierteste Formen möglich, die für herkömmliche Fertigungstechniken wie das Fräsen undenkbar wären.
Der 3-D-Druck im Pulverbettverfahren ist an sich nichts Neues. Damit Bauteile für ein großes Zivilflugzeug zu generieren, ist es schon. „Eine große Herausforderung bestand darin, die Material- und Bauteilkennwerte so zu untersuchen, zu definieren und immer wieder zu optimieren, dass wir den hohen Anforderungen der Luftfahrt gerecht werden“, sagt Anna Bauch. Deshalb nahmen die Teams auch von den Pulverkörnern bis hin zu den Oberflächeneigenschaften des finalen Bauteils alles genauestens unter die Lupe. „Die zweite Herausforderung bestand darin, dies auch reproduzierbar sicherzustellen“, erzählt sie weiter. „Denn wir mussten nachweisen, dass es sich nicht nur um einen Einmaleffekt handelt, sondern dass wir die Material- und Bauteilkennwerte immer wieder erreichen.“
LuFo hilft ungemein, dass die richtigen Partner für ein Projekt an den Tisch kommen
Der Aufwand und die Beharrlichkeit, mit denen die Teams ans Werk gingen, hat sich ausgezahlt. Die CFK-Integralspante aus IMPULS-Rasant fliegen mittlerweile serienmäßig im A350. Und aus ALM2AIR und anschließenden LuFo Projekten sind die ersten im metallischen Pulververfahren gefertigten Bauteile hervorgegangen, die Airbus in ein Zivilflugzeug einbrachte. 3-D-gedruckt fliegen heute beispielsweise die doppelwandige Treibstoffleitung für das Tanker Kit im A400M und der Hydraulikverteiler im Bremssystem des A320.
LuFo, meint Anna Bauch, hätte zu solchen Erfolgen maßgeblich beigetragen. „Ich bin ein Kind des LuFo“, sagt sie und lacht. „Während meiner Dissertation habe ich an einem Arbeitspaket für ein LuFo-II-Projekt gearbeitet, bin dadurch zu Airbus gekommen und habe dort gleich die technische Leitung eines weiteren LuFo-Projekts übernommen.“ Dabei hat sie bis heute immer wieder festgestellt: Das Förderprogramm macht es leicht, dass die richtigen Partner für Projekte wie IMPULS-Rasant oder ALM2AIR zusammenfinden. „Und durch die finanzielle Unterstützung bekommen wir die Möglichkeit, uns auch personell auf solche Themen zu konzentrieren. Das schafft einen nicht zu unterschätzenden Zeitvorteil.“
Text: Kai Dürfeld

Projektträger Luftfahrtforschung
Kontakt:
Airbus
Dr. Anna Elisabeth Bauch
E-Mail: anna.bauch@airbus.com
www.airbus.com