Joint project InnoTurbinE
The "Efficiency First" guiding principle set out in the 7th Energy Research Programme of the Federal Ministry of Economics and Climate Protection (BMWK) means making particularly efficient use of primary energy and thus conserving resources in the long term, but also drastically minimising CO2 emissions in the interests of environmental protection. In the power plant sector, this means on the one hand operating highly efficient plants and on the other hand closing the loop to renewable energies. Their volatile nature places ever greater demands on the electricity grid for geographical distribution and on storage to bridge the gap over time. To ensure security of supply and stabilise voltage and frequency, electricity generation using turbomachinery in conventional power plants will therefore continue to be necessary.
Accordingly, "With regard to fuel and load flexibility, the optimisation of processes and systems as well as the service life of the overall plant and its components, including thermodynamic and aerodynamic optimisations (increasing operating temperatures, optimisation of cooling systems)" is a development topic. In particular, this also means that future gas turbines should be able to utilise hydrogen-enriched fuels. Furthermore, this research project is intended to make a significant contribution to aerodynamic optimisation. Several work packages have been identified here, which should help to exceed current design limits in the area of both the compressor and the turbine with the aid of the latest methods.
Work packages
WP 1: Turbomachines for the H2 economy
Highly efficient gas-fired power plants in combined operation with steam turbines or integrated into CHP plants make a significant contribution to reducing greenhouse gases. Following the realisation of the coal phase-out, it is assumed that from 2038, Germany's electricity demand will only be covered by renewables and gas. However, as renewable energy sources become more widespread, sustainable energy storage will play a key role. Chemical storage makes an important contribution to solving the problems of seasonal bridging of longer periods of darkness in the winter half of the year. The Power-to-X principle is often mentioned here, whereby surplus energy can also be stored as fuel. Hydrogen is particularly relevant from an energy policy and technical perspective. In the area of hydrogen distribution and storage infrastructure, significant increases in efficiency and cost reductions will also make a major contribution to the provision of hydrogen as an energy carrier. This applies to the distribution and storage of both liquid and gaseous hydrogen. The hydrogen - compressed in gaseous form or cryogenically liquefied - can be stored, transported and used as a fuel in gas turbines, combustion engines or fuel cells to generate energy.
WP 2: Cycle-proof turbo components
The robust design of centrifugal compressors in early design phases and the broadening of the operating range (map) of centrifugal compressor stages for future use in the field of gas supply to power plants, gas storage, gas transport and storage of electrical energy (compressed air storage or thermal) is of central importance for the robust and dynamic operation of turbo components. In future high-efficiency gas turbines, which can guarantee highly flexible operation over a very wide operating range, aeromechanical vibration excitations caused by combustion, multi-stage interaction and blade flutter will become much more important and will even influence the design of the turbine blades, which are subject to the highest thermal and static loads. As the various excitations can no longer be completely avoided in the design, targeted damping optimisation is essential, which must be carried out integrally with the blade design and can only be achieved through multi-disciplinary optimisation. The precise prediction of natural frequencies and damping behaviour in the shroud area is of great importance for a wear assessment and, based on this, to increase the optimisation potential with regard to vibrations in the design in the future in order to reduce wear during operation. To this end, the functionality of simulation tools for non-linear structural dynamics must be further developed in order to be able to evaluate effects such as friction, impacting contact and micro-slip.
WP 3: Virtual product development under real conditions
Today, turbomachinery is being pushed ever closer to its design limits. Whereas in the past, uncertainties about the real conditions in the turbine were taken into account in the design by means of margins (safety factors/distances), today a conscious effort is being made to reduce these margins further and further. As a result, efficiencies can be increased even further, or modes of operation can be permitted that manufacturers were previously unable to guarantee. The margins taken into account in the design therefore serve to accept uncertainties. These uncertainties lie on the one hand in the fact that it is not known exactly how the machine will actually be loaded (uncertainties regarding physics), and on the other hand in the fact that it is not possible to predict 100% what the machine will look like after production (production tolerances). In addition, there are uncertainties regarding the operating mode that cannot be taken into account when calculating service cycles. The calculation and consideration of such uncertainties exceeds the tools and methods used today for the design and monitoring of turbomachinery. In recent years, as part of the general trend towards digitalisation, virtual development has produced ever better models and methods that can be used for the problems described above. In contrast to previous projects focussing on probabilistic methods, this work package simultaneously addresses all three points of uncertainty in the real conditions of turbomachinery operation, namely the physical and geometric as well as the interdisciplinary nature of the influencing phenomena. The ultimate goal is to predict the assessment of required service intervals in the sense of a digital twin by simulating the real operation of a compressor, for example, or the condition of sealing systems in parallel to operation with the help of such digital twins in the future.
Project structure

Facts and figures
Volumen
15.625 k€
Project duration
01.07.2020 - 30.06.2024
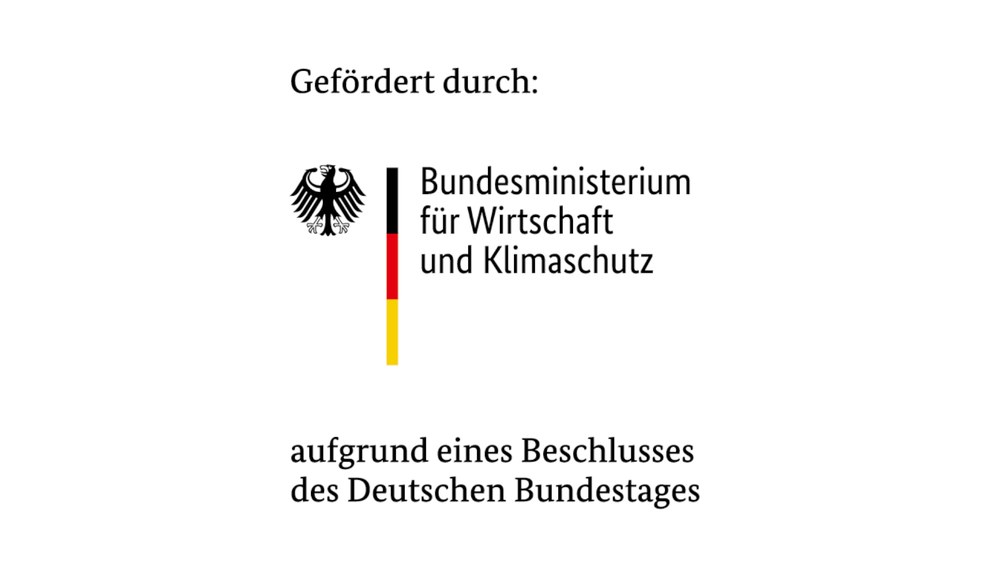
BMWK