Efficient flying – periodic pulses of air control flow over aircraft wings
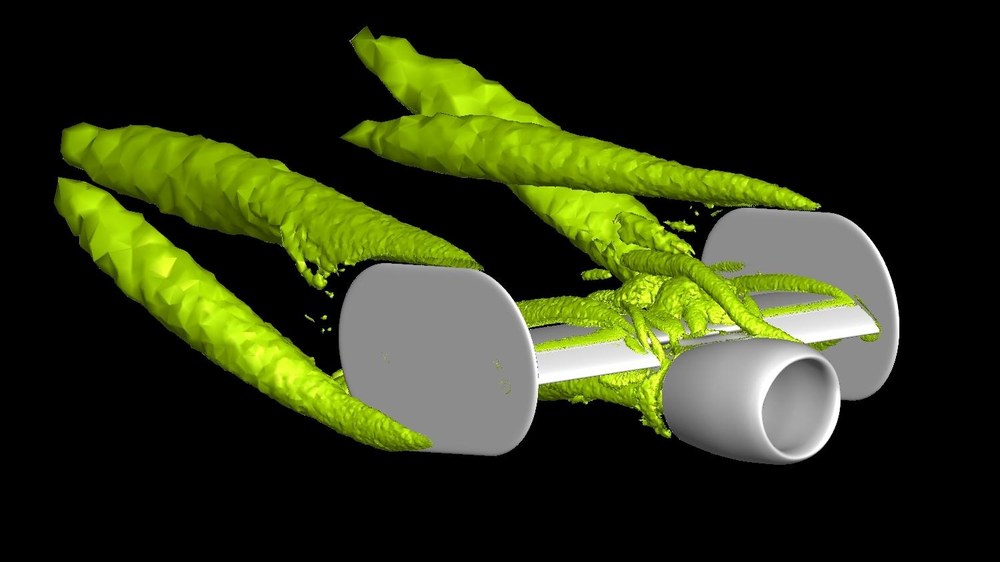
Larger and more powerful engines are making flying more efficient. These gigantic main engines take up more space on the wings of modern passenger aircraft. However, they influence the flow over the wing surface and reduce lift. Because of these large engines, aircraft must be flown faster, particularly during take-off and landing, to maintain lift and stability. With the development of even larger engines, longer airport runways will soon be needed. To avoid this, researchers at the German Aerospace Center (Deutsches Zentrum für Luft- und Raumfahrt; DLR) are working on a system that influences the airflow and thus increases lift.
Using compressed air to prevent stalling
The key to increasing lift is to blow out compressed air at particularly flow-sensitive locations. Together with Airbus and other European partners, DLR researchers have been studying this technology with the help of computer models as part of the EU 'Active Flow Loads and Noise Control on Next Generation Wing' (EU AFLoNext project) project. "By periodically expelling air at the leading edges of the aircraft wings through precise, narrow double slits, we can actively influence flow behaviour on the profile surface," explains Vlad Ciobaca from the DLR Institute of Aerodynamics and Flow Technology. The approach was developed at the Technische Universität Berlin and refined in several joint projects until it was ready for application. "We were able to demonstrate that local flow separations at the transition from the engine to the wing are almost completely suppressed," notes the aerodynamics specialist. The technology also works at the transition between the wings and the wing tips. The compressed air originates from actuator chambers that are embedded in the leading edges of the wings.
Reduced fuel consumption
Discussing the pulsed blowing technique, Ciobaca explains: "In this way, vortices are generated at the surface profile of the wing, which mixes the flow near the surface with the free flow. As a consequence, the maximum lift increases and drag decreases, resulting in a more efficient aircraft with lower fuel consumption and carbon dioxide emissions. At the same time, a machine with this technology can fly more slowly, so shorter landing distances are possible." In contrast to conventional flow control systems, the intermittently active flow control requires less air, is more effective and virtually maintenance-free. "The concept of intermittent trailing edge blowing has already been established, but it is only used in some research aircraft. We are the first to explore this form of active flow control at the complex engine-wing junction," says Ciobaca, adding: "This research is application-relevant and could mean major improvements for passenger aircraft."
Promising results for the new technology have also recently been acquired as part of the joint project MOVE.ON, which was led by Airbus. Together with the Technical Universities of Berlin and Braunschweig, researchers successfully tested active flow control on a model of the outboard portion of a wing in the low speed wind tunnel (DNW-NWB) at the DLR site in Braunschweig. The MOVE.ON project was funded as a part of its aviation research programmes by the German Federal Ministry for Economic Affairs and Energy.
Technology ready for production
To develop the system to the extent that it could be incorporated as standard in the next generation of aircraft, testing will soon move on to the next stage. Current plans for the coming year include the AFLoNext research group traveling to Moscow where they will test localised separation control on an almost full-size wing with an engine in one of the world's largest wind tunnels, the Wind tunnel TsAGI T-101. The next step towards verifying this technology, according to the researchers involved, would be to conduct flight tests on an aircraft.