DLR examines the effects of different engine configurations
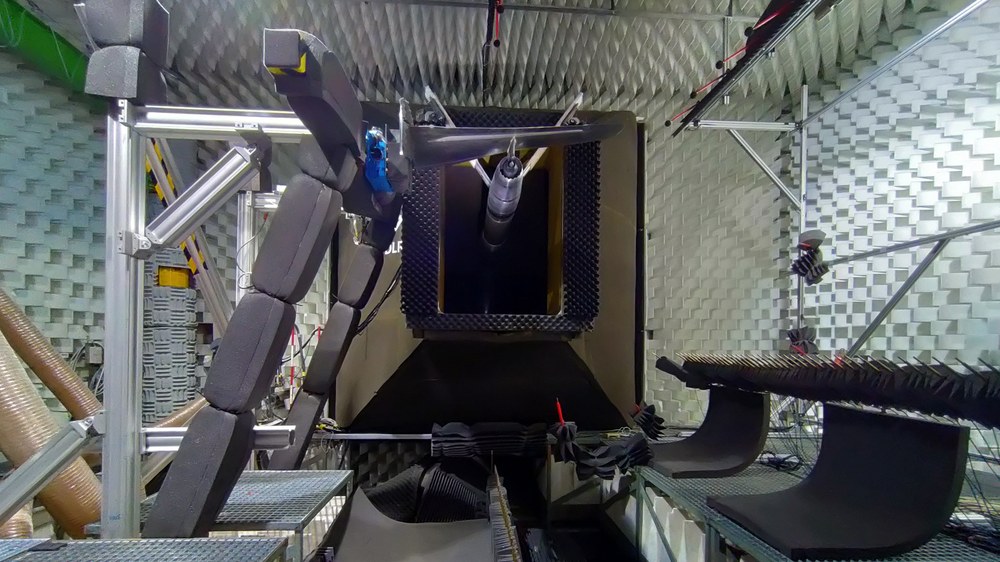
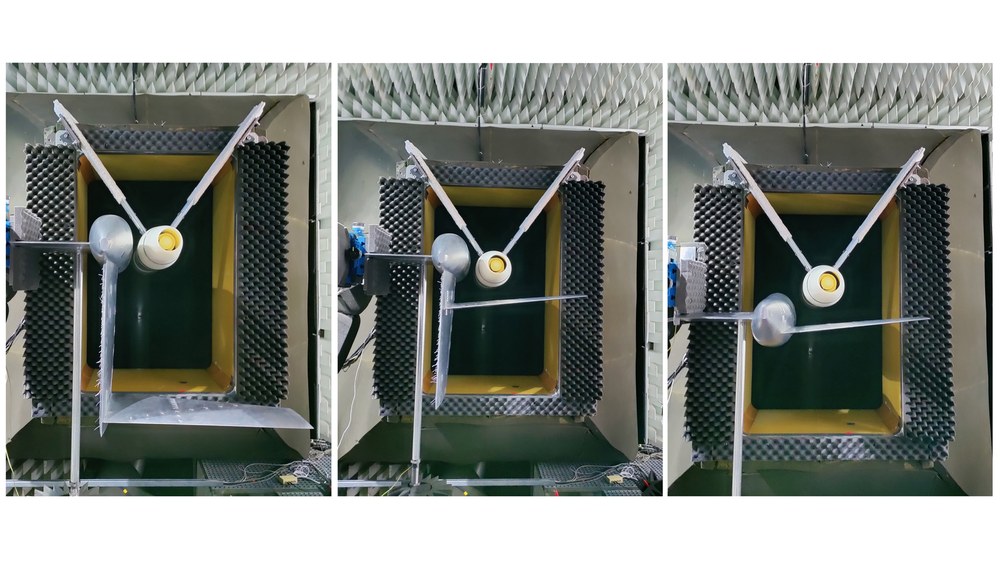

- As part of the DJINN project, DLR has been conducting tests on the interaction between engines and aircraft in different configurations.
- The researchers have been investigating new configurations and materials in order to reduce noise from engines.
- Porous 'meta' materials reduce pressure fluctuations in the turbulent boundary layer.
- Focus: Aeronautics
Wind is blasting at 60 metres per second through a dark duct almost one metre wide and 1.2 metres high. Just outside it hang pieces of equipment, racks and microphones. The Aeroacoustic Wind Tunnel (Aeroakustischer Windkanal Braunschweig; AWB) operated by the German Aerospace Center (Deutsches Zentrum für Luft- und Raumfahrt; DLR) in Braunschweig is not one of the largest examples of its kind, but its design puts it at the very forefront of European aeronautics research. As part of a large-scale EU project funded by the Horizon 2020 programme, DLR has been carrying out tests in the AWB on the interaction between engines and aircraft in different configurations.
For the EU project Decrease Jet-Installation Noise (DJINN), researchers used the AWB to investigate aircraft noise. "We are focusing on aircraft noise, which is primarily generated by the interaction between the engines and the aircraft," says Christian Jente of the DLR Institute of Aerodynamics and Flow Technology. Larger and more powerful engines on aircraft fuselages and wings of the same size cause more noise due to the interaction of the airflow around them. "With that in mind, the DJINN team looked at new configurations and materials," says Jente.
Putting two aircraft concepts to the test
The researchers conducted the experiments in the wind tunnel in order to investigate two different aircraft concepts – an aircraft where the engines are installed beneath the wing, like a typical large commercial airliner, and a typical business jet, where the engines are located at the tail. For the latter, they set up several different test series: "We performed acoustic measurements on three different tail units for the business jet," says Jente. "Two conventional tailplanes in a cruciform and T formation, and a U-tail, where the horizontal stabiliser is designed to muffle the engine noise." The aim here was to evaluate the acoustic benefits and drawbacks of different configurations and measures. Among other things, the researchers examined how the surface of the aircraft fuselage is stressed by acoustic vibrations – in other words, how 'acoustic fatigue' affects the material.
For this purpose, researchers from the DLR Institute of Propulsion Technology set up two linear microphone arrays more than three metres long in the AWB. This arrangement of microphones allowed them to calculate the precise locations and direction-dependent intensities of the sound sources at the engine exhaust, on the fuselage and on the wing. In addition to the linear microphone arrays, far-field microphones on the ceiling measured the sound dispersion in different directions, as this can vary greatly depending on the tail unit concept.
Porous materials reduce noise
In their wind tunnel setup for the commercial aircraft, the researchers carried out another experiment – they chose a porous material for the landing flaps. In other tests, DLR has demonstrated that porous materials have positive acoustic properties. When air flows over porous materials, pressure fluctuations in the turbulent boundary layer are reduced. This means that these are not converted into sound at the trailing edge of the landing flap. "This was the first time that porous landing flaps have been tested in this configuration at high speed," says Jente. Until now, only simplified geometrical configurations have been investigated. Prototype 3D models have never been tested before under realistic operating conditions in the wind tunnel. "We have shown that complex models can also be made from these kinds of 'meta' materials, which gets us closer to industrial applications."
This marked a decisive success for the aeroacoustic researchers. They feel certain that porous or 'meta' materials will play an increasingly important role, as these artificially produced materials have physical properties that do not occur in nature, thus enabling new types of applications. For example, depending on the required capability, function or research purpose, they can influence light and sound waves.
The two DLR institutes are now evaluating 400 gigabytes of microphone data. The results will help them develop technologies that can reduce the noise levels of future aircraft. The researchers spent several years preparing the measurements in conjunction with a large number of project partners.
The DJINN project
The DJINN (Decrease Jet-Installation Noise) project is part of the EU Horizon 2020 Framework Programme for Research and Innovation. It runs from June 2020 to December 2023.
Project partners: Airbus, CFD Berlin – CFD Software Entwicklungs- und Forschungsgesellschaft mbH, CERFACS (F), CNRS (F), Dassault Aviation, DLR Institute of Aerodynamics and Flow Technology, DLR Institute of Propulsion Technology, Imperial College (UK), ONERA (F), Queen Mary University (UK) Rolls-Royce Deutschland, Safran Aircraft Engines, University of Southampton (UK), Von Karman Institute (BE).