A small taste of the future
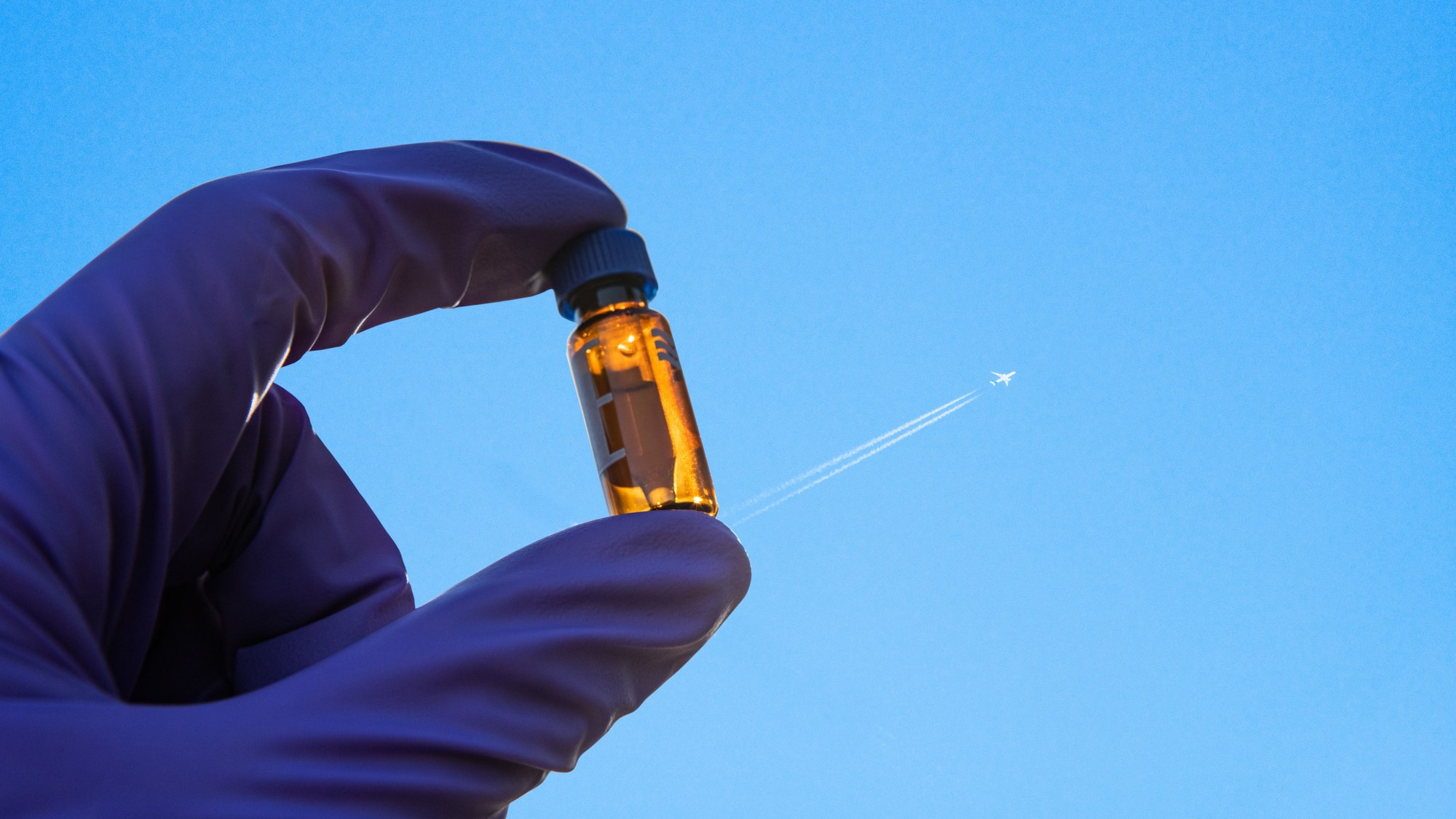
What do new aviation fuels and good wine have in common? They are both more diverse and consist of more components than most people realise – and even the smallest variation can spoil everything. For this reason, researchers at the DLR Institute of Combustion Technology in Stuttgart have developed a test method for new fuels, referred to as prescreening. Thanks to modern chemical analysis methods – similar to those used for wine – less than a millilitre is sufficient to characterise the fuel, before evaluating it in detail using modern machine learning methods.
When Hannes Lüdtke wants to examine a new fuel, he does not reach for a tap or can. Instead, the doctoral student takes a pipette and transfers the fuel into amber glass vials that measure just half the length of his little finger. These vials hold just 300 microlitres – one-sixth of a standard tube of baking flavouring. The injection volume is even smaller – one microlitre. From this tiny amount of the clear, almost odourless liquid, the chemist can determine the composition of the fuel at the molecular level. "We use two dimensional gas chromatography for this. It is a powerful method for analysing complex liquids such as fuels using only minute samples," says Lüdtke.
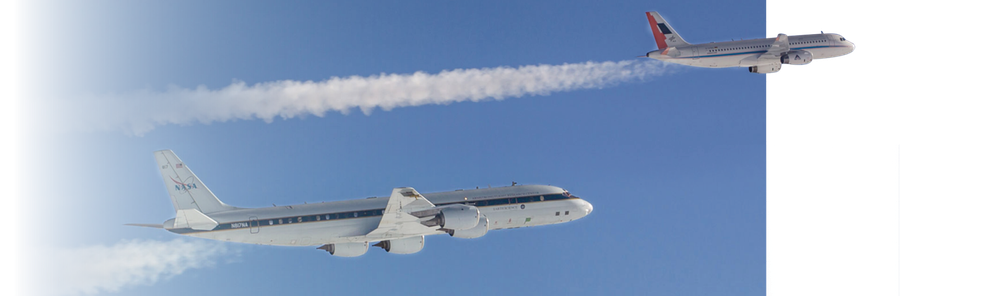
DLR / NASA / Friz
Profiling fuels
However, this step is not sufficient to determine whether the fuel is suitable for safe aircraft operations. To achieve this, the researchers must also determine the ratio of the groups of substances to one another. Only then does a profile of properties emerge – similar to the taste of a wine. Aspects such as viscosity, density, behaviour at low temperatures and high-altitude relight are key factors for approval. To determine these properties, researchers at the Institute of Combustion Technology examine the results of the gas chromatography procedureusing specially developed machine learning models. "These are the real key to success," says Senior Scientist Uwe Bauder. "The models help us to reliably predict the properties that result from the composition of the fuel."
The development of prescreening – also referred to as technical fuel assessment – marked a milestone towards making sustainable fuels market ready. The test procedure precedes the approval process. This avoids manufacturers having to invest millions of euros in setting up production for test batches of hundreds of thousands of litres, only to find that they are producing a fuel that is not ready for approval. The idea of prescreening first arose in 2017 in the EU JETSCREEN project, according to Bastian Rauch, who was a group leader for sustainable fuels at the Institute until the end of June and coordinated this project. At that time, fuel could only be evaluated using complex tests in combustion chambers, such as those conducted at the Institute of Combustion Technology. Then, however, they would have needed at least 200 litres to carry out such tests, as Rauch recalls. This requirement was already proving a major obstacle for companies intending to develop a fuel and set up production, as they might only produce a few millilitres per day or even per week.
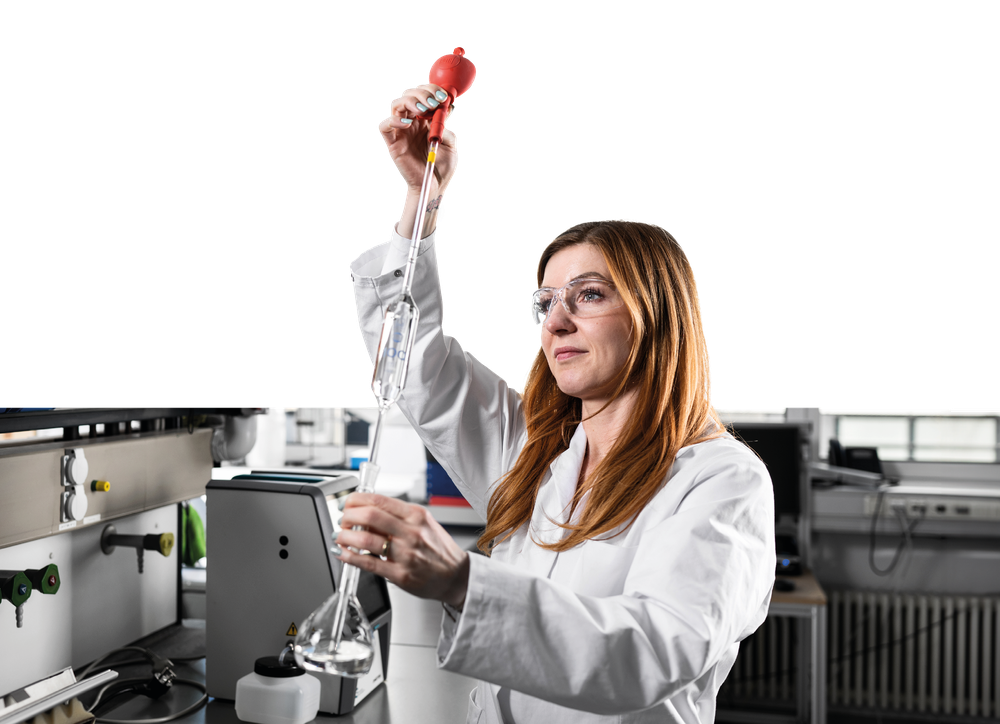
An effective testing method from Stuttgart
As a result of these difficulties, the researchers in Stuttgart came up with the idea of developing a simple but effective test procedure – prescreening – and conducting it before the approval process. As Josh Heyne was working on this problem as part of the US National Jet Fuels Combustion Program at the same time, the two organisations decided to collaborate. All those involved are still benefiting from the success of this cooperation today.
The SimFuel database was created in Stuttgart as an outcome of the project. It now contains data from more than 15,000 conventional jet fuels, over 450 new fuels and a vast array of analysis of the most important molecular groups in these candidates. Quite a few of these new fuels have come from research projects that made their data available. "The database is a real gem," says Uwe Bauder, whose team works on the machine learning models. "It enables us to keep on developing the methods and models and give fuel and engine manufacturers increasingly detailed feedback."
The experts at DLR use self-learning algorithms to couple experimental investigations in the field of chemical analytics. Bauder's team optimised a series of machine learning models to predict the most important material properties. These models are trained with data from the SimFuel database and are then used to predict the properties of new candidates based on the detailed gas chromatography results. Visualisation of the results in the form of complex, specially developed diagrams makes it possible to see what behaviours the fuel will later exhibit. Most importantly, it reveals whether these properties lie within or outside the limits specified by the certification authority.
In recent years, the Stuttgart team has gained a lot of experience in evaluating new fuels. Many research projects have had samples of their products analysed at the Institute and were able to optimise their processes on the basis of the feedback. The evaluation of numerous new fuels, combustion chamber tests and collaboration with other DLR institutes have shown that the predictions made by the prescreening process are indeed accurate.
International demand
Four to six manufacturing companies now have their developments tested at DLR in Stuttgart each year. Their production paths vary substantially. The Institute's customers include start-ups that rely on the Fischer-Tropsch process, in which fuels can be produced with the help of electrolysis. One example is INERATEC GmbH, the most successful start-up in Germany to date. The DLR team is working on numerous projects with this spin-off from the Karlsruhe Institute of Technology (KIT). Other start-ups use biomass as a raw material, for example XFuel, which is based in Dublin and has a production facility in Mallorca. Large corporations such as Neste and OMV also use the prescreening process to optimise their new developments. These examples show the enormous range of technical solutions that fall under the term Sustainable Aviation Fuels (SAFs).
"The prescreening process was a valuable aid for all of the manufacturing companies," says Uwe Bauder, "because it enabled them to make corrections to the product and the production process at a very early stage." Bauder acknowledges that the procedure does not guarantee successful certification, but notes that prescreening has significantly improved the chances of fuel candidates being successfully certified.
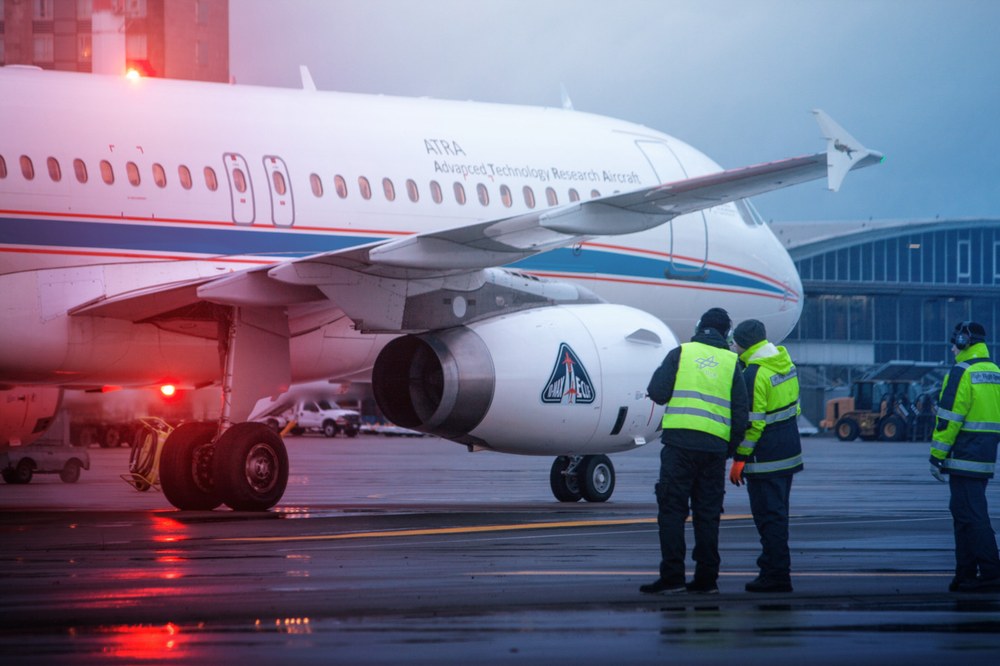
At present, ASTM International (formerly the American Society for Testing and Materials), based in Pennsylvania, USA, is the only organisation in the world that can certify both bio-based and electricity-based alternative fuels. In this process, it involves the manufacturers of all aircraft components that come into contact with a fuel – and there are quite a number of these. Therefore, each of these companies must test a candidate fuel as part of the certification process. If each country had its own certification office, such a process would prove completely unmanageable, so it was agreed to handle all the tests at one approval centre. To date, DLR is the only research institution in Germany that can effectively implement such an approval process.
According to Bastian Rauch, however, large companies with the necessary capabilities are now seeking to establish prescreening themselves. He sees this as a positive thing: "If you think technology transfer through, this is the next logical step in the development."
Moving away from fossil fuels
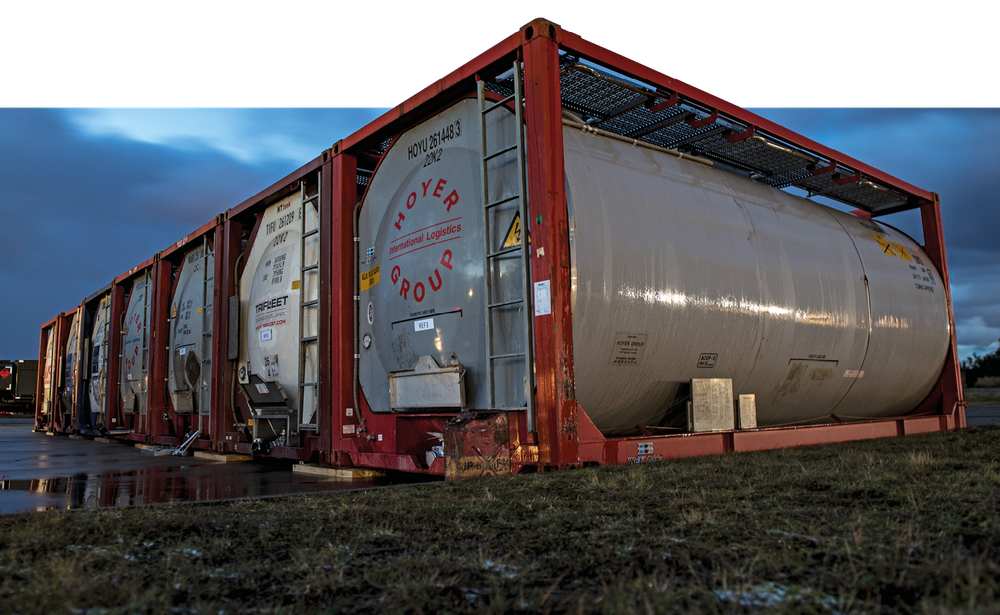
DLR (bearbeitet)
A lot has happened since the very first approval of a Fischer-Tropsch manufacturing route in 2009, not least due to the advent of prescreening. In the beginning, says Patrick Le Clercq, a Head of Department at the DLR Institute of Combustion Technology, the scientists endeavoured to imitate kerosene as closely as possible. Any new fuel had to be measured against Jet A-1, the most common fuel for turbine engines. Nowadays, researchers and manufacturers are able to think much more freely, and the idea of what a fuel should look like is increasingly geared towards the challenges of the future instead of the fossil model of the past.
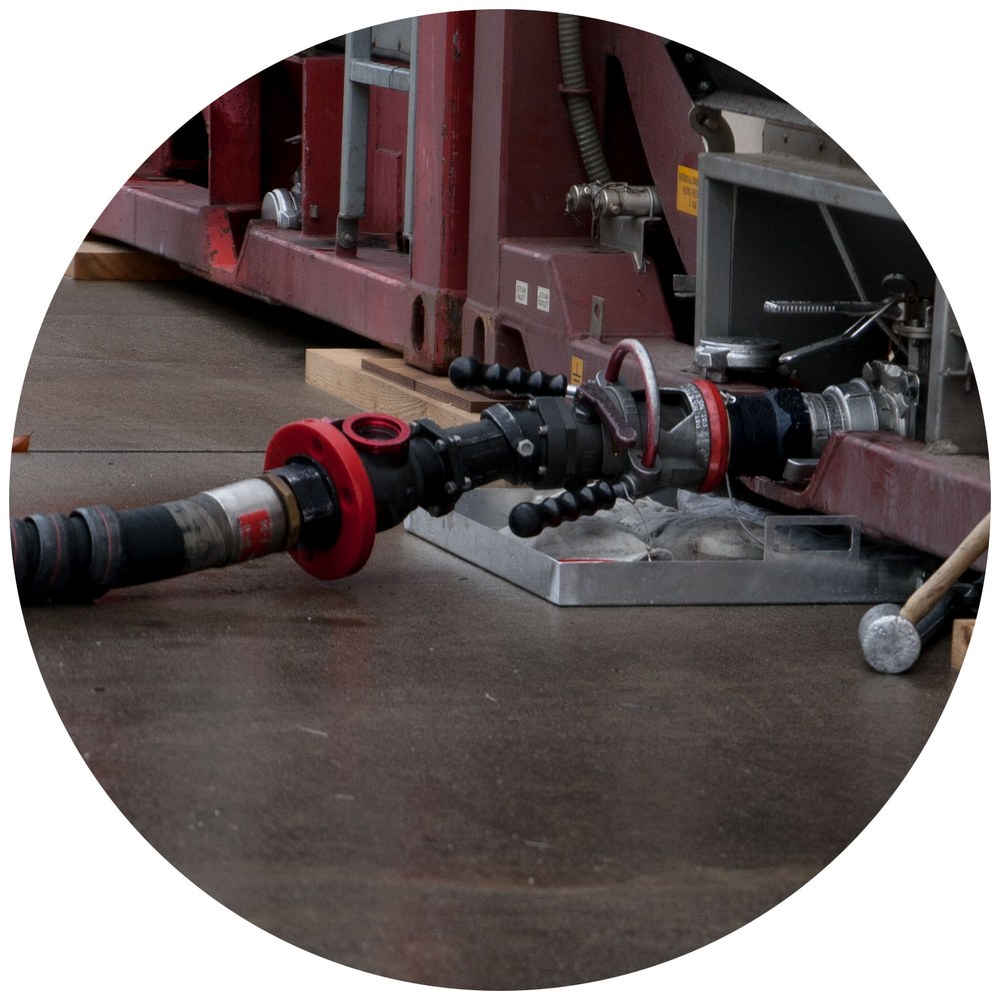
Over the course of several successful Emission and Climate Impact of Alternative Fuels (ECLIF) flight measurement campaigns, the researchers from Stuttgart demonstrated that the prescreening process can also be used creatively. During these test flights, which have been carried out since 2015, they examined the effect of synthetic fuels on the climate with colleagues from the DLR Institute of Atmospheric Physics. In 2018, for example, kerosene was mixed with a fuel made from different compositions of fats, referred to as Hydroprocessed Esters and Fatty Acids (HEFA). This was the first time that a fuel had been designed based on the ideas of the Stuttgart researchers, with a reduced proportion of aromatics. The results exceeded their expectations.
Le Clercq's team is now keen to design a fuel that burns in an almost climate-neutral way. At the same time, Uwe Bauder is working with Andreas Meurer from the DLR Institute of Networked Energy Systems to design and optimise fuels and their production as a completely digital process. In the next step, Le Clercq wants to rethink not only the fuel, but also the engines. He is expecting major progress from these efforts at co-optimisation together with engine manufacturers.
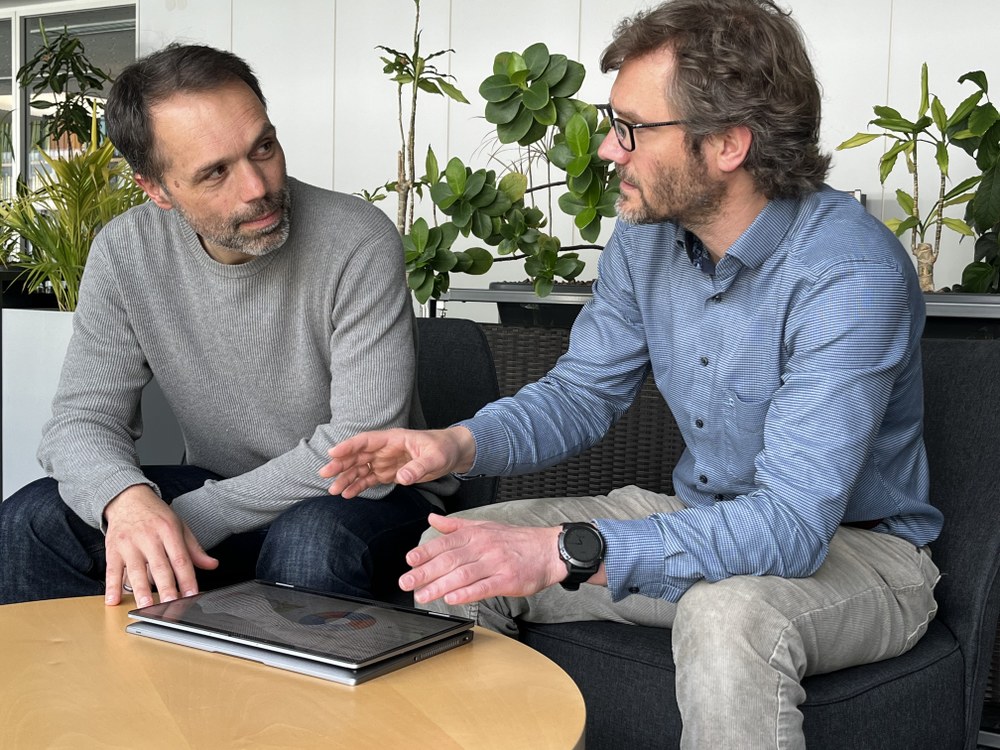
Synthetic fuels have great potential. The results of the research conducted during the ECLIF flight campaigns showed for the first time that a reduction in aromatics results in lower soot emissions and thus fewer condensation trails. This saving could increase to up to 80 percent – a particularly significant development, given than non-carbon-dioxide effects account for the largest proportion of the climate impact of aviation. This is especially true if it takes effect in the crucial next few years, so rapid market launch is important. By developing the Technology Platform Power-to-Liquid (TPP), DLR is making an important contribution towards the introduction of this process. The facility will be set up at the Leuna Chemical Complex in Saxony-Anhalt. It is expected to produce electricity-based fuels for research purposes on a semi-industrial scale from December 2026, paving the way for industrial manufacturing companies. At the same time, scientists will be able to test completely new ideas there in the experimental production branch.
When Patrick Le Clercq uncorks a bottle of good French red wine in the evening, decants it and pours himself a glass, he often thinks about the many unanswered questions in his research projects – and is reminded that at least as much work goes into a good fuel as into a good wine.
An article by Anja Tröster from the DLRmagazine 173