Unleashing the digital nodes

The railway network is becoming increasingly congested, particularly at its nodes. It is also the case that in the coming years, more people and goods are to be transported by rail than ever before. Great hopes are being pinned on digitalisation to find a solution and accommodate rising demand, particularly in the area of control and safety technologies. DLR is playing a key role in this process of transformation, offering many years of experience and know-how in transport research and unique state-of-the-art test facilities for digital certification and ongoing development of components and systems.
Railway nodes, or junctions, are critical points where multiple lines converge or intersect, making them essential for the smooth operation of the rail network. Nodes are often located near major railway stations and play a key role in determining the network's overall capacity – specifically, how many trains can be managed and where within a given time frame. Expanding capacity at railway nodes is a complex task. The addition of new tracks or points often proves challenging due to existing infrastructure such as buildings in city centres, tunnels, bridges or other unique geographies in certain areas. As notable examples like the Hohenzollern Bridge in Cologne or the Stuttgart basin demonstrate, such projects are typically time-consuming.
A digital node refers to, for example, a large railway station, where all operations and maintenance are managed digitally.
The digitalisation of the railway network, particularly at nodes, holds great potential for increasing its performance, with estimates suggesting that capacity could be boosted by 20 to 35 percent. To achieve this, digitalisation will require the conversion of nodes to digital systems, carried out in stages, ideally without disrupting ongoing operations.
Digital railway nodes: virtual control of operations and maintenance

"A digital node refers to, for example, a large railway station, where all operations and maintenance are managed digitally," explains Michael Meyer zu Hörste from the DLR Institute of Transportation Systems in Braunschweig. With over twenty years of experience in railway research, particularly in control and safety technology, he is well versed in the digital transformation of railway systems. "A digital node also generates vast amounts of data, which can be systematically collated and analysed to improve the functionality of individual components or the entire node – including with the use of artificial intelligence," Meyer zu Hörste adds with an eye on the future. In the case of predictive maintenance, real-time data can be used to forecast when components are likely to wear out, allowing for their timely replacement. This proactive approach would help minimise downtime and ensure smoother operations.

Deutsche Bahn
All aboard a very safe mode of transport!
Despite high speeds and long braking distances, rail travel remains one of the safest modes of transport. This is largely due to the fixed paths provided by tracks and the advanced control and safety technologies in place. Unlike driving a car, where you react to obstacles as they appear, operating a train requires action well before any potential hazard is even visible. Rail travel follows its own unique logic, with a constant dialogue between train drivers and signallers. Every railway line has a precise route profile, which contains critical information such as speed limits, the locations of signals and points, and designated stopping points. Train drivers must be thoroughly familiar with the route and never operate on unfamiliar lines.
Railway lines are divided into what are called block sections, and only one train is allowed to travel in each block section at a time. The length of these sections can vary from a few hundred metres on busy lines to several kilometres on quieter routes, with shorter sections typically found near stations. Before entering a block section, drivers must receive authorisation from the signaller. Once within a section, drivers have some flexibility, based on the route profile, to adjust their speed, accelerating or decelerating as necessary. The block section system has been in place now for decades and is considered very safe. It is computer-controlled and relies on a combination of mechanical, electrical and radio components. However, the system has its limitations. It lacks dynamic flexibility, as the only information available is whether or not a train is in a block section, but not its precise location. To increase the capacity of railway lines, block sections would need to be made smaller, which in turn requires exact knowledge of a train's position within it. This is where newer technologies like ETCS come into play, offering improved localisation and communication capabilities.
ETCS: four letters that herald the digital railway
The European Train Control System (ETCS) plays a pivotal role in the digitalisation of railway nodes and the broader rail network. The initial concepts for digitalising and standardising rail transport in Europe began to take shape as early as the late 1980s, focusing on train radio, traffic management and train control systems.

Adobe Stock/Andy Ilmberger
The ETCS ensures safe operations by automatically applying a train’s brakes or stopping it altogether if it exceeds speed limits or enters an unauthorised section of track. Historically, Germany and Europe have used a wide range of systems from various manufacturers for these tasks, making it essential to rigorously test and certify the interoperability of all components between trains and their infrastructure.
The ETCS has been designed to ensure a consistently high level of safety across Europe's railways while increasing network capacity. This requires highly precise localisation and enhanced communication between rail vehicles, infrastructure and traffic management systems. The ETCS also serves as the foundation for highly automated train operations. The rail networks in Switzerland and Luxembourg are almost entirely equipped with ETCS, and parts of Germany and many other European countries already operate some ETCS-enabled lines and vehicles.
However, expanding ETCS across more routes and so increasing capacity and flexibility comes at a price. "The German rail network alone covers nearly 40,000 kilometres, with more than 50,000 passenger and freight trains running on it every day – and these numbers continue to grow," continues Meyer zu Hörste. “Equipping every route and train with the highest level of ETCS may not be possible or even necessary, but it remains a mammoth task nonetheless for all involved. Drawing on our scientific research and DLR's extensive experience in railway studies, we can advise stakeholders from industry, policymakers and the public, highlighting practical options for action," he concludes.
The ETCS level
The European Train Control System (ETCS) has various functional levels, each defining how train movement and control are managed and monitored. In addition to Levels 1 and 2, there is also 'Moving Block' mode, in which the distances between trains are automatically detected. This allows trains to travel with shorter gaps between them, thereby increasing the capacity of the route.
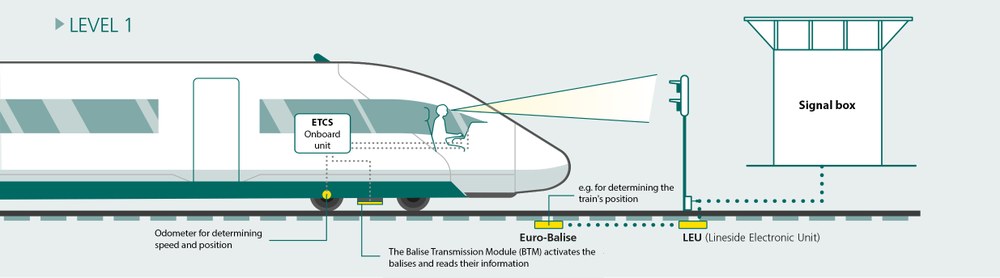

DLR RailSiTe test laboratory: digital systems can also be tested digitally
Railway networks are highly complex ecosystems subject to strict safety requirements, making the testing and approval of new components and systems equally complicated, not to mention extremely expensive. Conducting real-world tests on railway infrastructure is often time-consuming and limited due to operational and cost constraints. For over a decade, DLR has been researching and testing concepts in its RailSiTe to address these very challenges, aiming to accelerate the deployment of new control and safety systems. "We digitally simulate the entire railway system in detail,” explains Lennart Asbach, Head of the Research Verification and Validation department at the DLR Institute of Transportation Systems. "This includes the train vehicles themselves, the control and safety technology on the tracks and in the signal boxes, the track infrastructure and the communication interfaces between train and track."
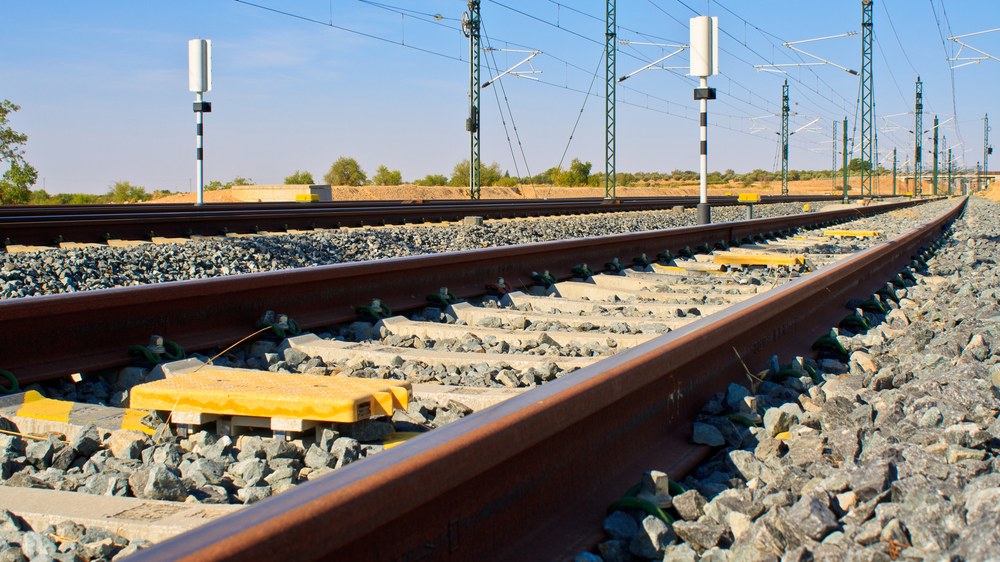
Adobe Stock/alvaro
One component that Asbach's team has already thoroughly tested is the ETCS onboard unit, which monitors trains and continuously exchanges data with the track. In the Deutsche Bahn network, over 13,000 ETCS balises are embedded in the track bed. These small yellow devices transmit crucial information to locate a train and, in some cases, to authorise its movement to the next section of track. Balises must always function reliably with trains from different manufacturers, ensuring for example that no interference occurs from nearby tracks. DLR researchers not only test the onboard ETCS computers but also the balises themselves.
Another key focus is developing test methodologies and the automation of these tests. "Our goal is to test and certify digital systems like ETCS entirely digitally," says Asbach. "Automating these processes can make testing faster, more reliable and more reproducible." For instance, the time required to test onboard train computers has already been cut in half.
Pilot project: Stuttgart Digital Nodes
Large railway nodes involve an almost unmanageable number of interconnected components. For these systems to function properly, every small part must be precisely positioned and operate as planned. The digitalisation of such railway nodes is highly complex, especially when carried out during active operations. 'Stuttgart Digital Nodes' (DKS) is a key element of the Stuttgart 21 project which aims to remodel the city’s main railway station and construct a new line to Ulm. For the first time, Deutsche Bahn is equipping a major railway node with digital control and safety technology. This will involve gradually upgrading approximately 500 kilometres of track in the greater Stuttgart area, including the S-Bahn network, with ETCS, digital signal boxes and other advanced technologies. Alongside the infrastructure upgrades, all trains using the DKS – around 600 in total – will also need to be retrofitted. These measures are intended to reduce the intervals between trains, particularly on the busy main S-Bahn line in Stuttgart.
Turning the dial to increase capacity

The transition to the ETCS is a long-term project at both national and European levels. To support this transition, DLR is carrying out operational simulations of rail transport to identify ways of improving capacity. "Although the railway system is highly complex, it can now be effectively modelled mathematically and simulated on computers," explains Christian Meirich, the Railway Operations Group Leader at the DLR Institute of Transportation Systems. The team also uses the RailSiTe lab to conduct these simulations, where they model both current and future railway systems, including automatic train operations. By adjusting specific parameters, such as transmission and signal-switching times , train schedules, delays, punctuality targets and even weather conditions, the team is able to explore many different scenarios. "We develop scenarios that demonstrate what’s possible under given conditions," Meirich continues. "This helps us identify ways to further improve system capacity." Testing these variables in the real world would be impossible due to the complexity involved, but simulations offer a reliable alternative. In railway operations, small time differences can have a significant impact. For example, if a train spends three minutes at a station, that adds up to 20 possible trains per hour. Increasing that stop time by just one minute then reduces a station’s capacity to just 15 trains per hour. On some routes, this difference could determine whether a train runs every half hour or only once an hour
Both Lennart Asbach and Christian Meirich are confident that DLR's simulation-based solutions are just as good as reality. "We are already testing, in a virtual environment, whether a train will be able to travel across Germany and Europe in the future ," says Asbach. “By doing so, we can provide manufacturers and operators with targeted support in addressing the challenges of tomorrow's rail system."
An article by Denise Nüssle from the DLRmagazine 176