The mechatronic running gear for the first journey in milligravity
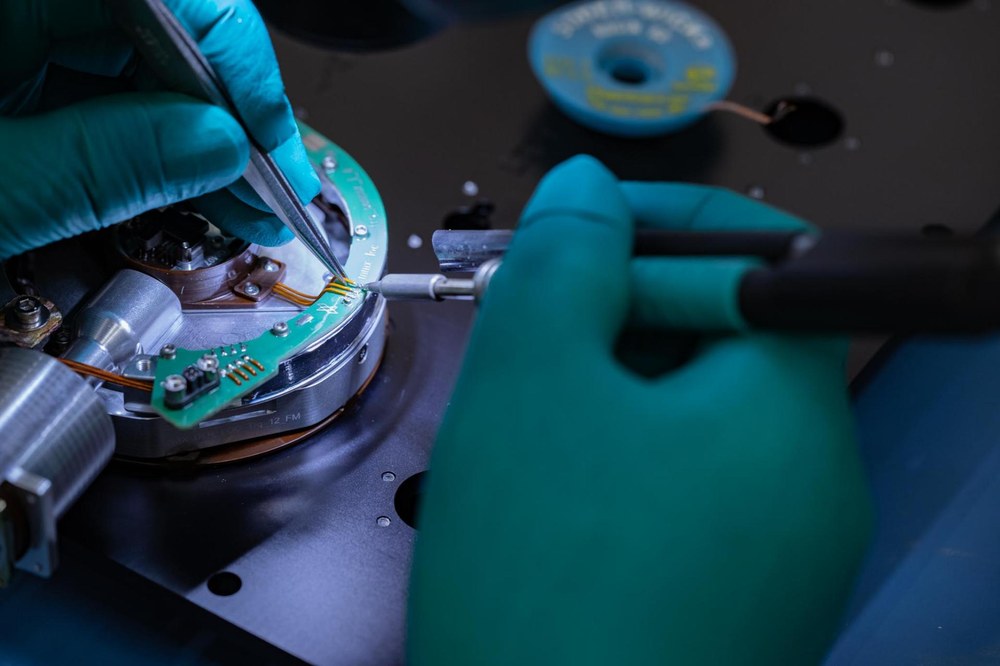

The mechatronic chassis – also referred to as the locomotion system – for the four-wheeled MMX rover IDEFIX is being developed, built and tested by two DLR institutes – the Institute of Robotics and Mechatronics and the Institute of System Dynamics and Control. The MMX rover will be the first robot to move in such low gravity. So far, rovers have only travelled on the Moon and Mars, where they have experienced one-sixth and one-third of Earth's gravity, respectively. By contrast, the gravitational pull on Phobos is only about one two-thousandth of Earth's gravity, which is referred to as milligravity.
Low gravity and unknown territory
The MMX rover, which has a mass of approximately 25 kilograms, will therefore only experience gravitational forces equivalent to that of a large grape on Earth. While a fall from a height of one metre on Earth takes only about 0.5 seconds, it takes 25 seconds to touch the ground on Phobos. In addition to the gravitational force, however, the rover must also contend with the ground resistance force. This force can vary from close to zero to several newtons, although the ground characteristics responsible for this are largely unknown so far. The wheels and shoulder motors therefore have a very high reduction ratio of over 1:2200 in order to provide a high torque.
On Phobos, this means that the rover has to move very slowly so that it does not fall over in curves or on bumps. Its normal speed will therefore be one millimetre per second. So, to travel from one goal to the other on a soccer pitch, it would need about 29 hours. At the maximum speed of approximately 0.5 centimetres per second, drifting and wheel lift-off can already occur on uneven surfaces, as is usually the case with rally cars.
The effects of low gravity mean that realistic tests on Earth are not possible. For this reason, a sophisticated computer simulation of the rover's dynamics and ground contact mechanics was of central importance for its development.
Functions of the running gear
The locomotion system must be able to perform additional functions besides simply driving straight ahead. Immediately after landing, the rover must first 'stand up' – in other words, upright itself. In order to be as compact as possible before release by the exploration module and to withstand the stresses that occur during landing, the legs and wheels on both sides of the rover are folded in. Once the rover has come to rest on the surface of Phobos, the legs are unfolded in a specific sequence so that the rover's wheels are on the ground and its solar panels point upwards.
The Sun shines only relatively weakly on Phobos. To cope with the limited area of the solar panels, the running gear can tilt the entire rover. Together with a Sun sensor, this makes it possible to point the rover optimally towards the Sun. In addition, the running gear can also increase or decrease the distance between the rover and the ground, which is necessary, for example, for the experiments with the Raman spectrometer.
Finally, the rover should be able to drive forwards and backwards, handle curves and turn on the spot. For reasons of space, the wheels are not steerable; the control of the chassis for curves and turns works – as with a tracked vehicle – by adjusting the differential speeds between the left and right wheels.

The running gear itself consists of four 'Loco modules', each comprising a rotating leg, a wheel and a highly integrated shoulder assembly with motors, gears, sensors, electronics and heaters. Hold-Down and Release Mechanisms (HDRMs) keep the legs and wheels in the folded position in the spacecraft and for landing on Phobos before a short power pulse releases the running gear.
Inside the rover is an electronics box that houses all the analogue and digital electronics, including the motor drives, analogue-to-digital converters and a Field-Programmable Gate Array (FPGA) that runs the specially developed firmware. The FPGA allows a fast clock rate for motor control and sensor readout, and also establishes communications with the main computer.
More complex functions, such as the kinematics control of the running gear, are executed in a software partition specially developed by DLR directly on the rover’s main computer, which is provided by the French partner Centre national d'études spatiales (CNES).
Development and testing of the running gear
The locomotion system for the MMX rover is a completely new development, although for some components it was possible to draw on experience from previous missions, such as the MASCOT lander on the Hayabusa2 mission. Because of the many new developments, it was necessary to build three prototypes of the landing gear and test them extensively. After about three years of development, the final design was ready and the models for qualification and flight could be built. For the actual qualification of the locomotion system, tests were then carried out in the expected mechanical, electrical and thermal environment. Finally, the necessary performance and durability were proven in performance and life tests, so that after about 150 laboratory days and over a kilometre travelled, the running gear is now ready for its mission on Phobos.
MMX – Martian Moons eXploration
MMX is a mission of the Japanese space agency JAXA with contributions from NASA, ESA, CNES (the French space agency) and DLR. CNES (Centre National d'Études Spatiales) and the German Aerospace Center (Deutsches Zentrum für Luft- und Raumfahrt; DLR) are jointly contributing a 25-kilogram rover to the Martian Moons eXploration Mission (MMX). The Franco-German MMX rover is being designed and built under the joint leadership of CNES and DLR. In particular, DLR is responsible for the development of the rover's landing gear, including the lightweight body, as well as the entire uprighting and locomotion system. DLR is also contributing the connection adapter to the MMX spacecraft and providing a Raman spectrometer and a radiometer as scientific experiments. These will analyse the surface composition and texture on Phobos. CNES is making significant contributions with camera systems for spatial orientation and exploration on the surface, as well as for the study of mechanical soil properties. CNES is also developing the rover's central service module, including the on-board computer and the power and communications system. After the launch of the MMX mission, the rover will be operated by CNES control centres in Toulouse (France) and DLR in Cologne (Germany).
For DLR, the institutes of System Dynamics and Control, Composite Structures and Adaptive Systems, of Space Systems, of Space Research, for Software Technology and the Microgravity User Support Center (MUSC) are also involved under the leadership of the DLR Institute of Robotics and Mechatronics.
The MMX mission is a continuation of an already long-standing successful cooperation between JAXA, CNES and DLR. It builds on the previous mission Hayabusa2, in which JAXA sent a spacecraft to the asteroid Ryugu with the German-French MASCOT lander on board. On 3 October 2018, MASCOT landed on Ryugu and sent spectacular images of a landscape ridden with boulders and rocks, and virtually no dust. Hayabusa2 collected samples from Ryugu and brought them to Earth on 6 December 2020.