Computer Simulation

The Computer Simulation department develops efficient and high-precision numerical methods for the calculation of complex flows with combustion.
The main tool is the in-house code ThetaCOM developed at the institute. The main focus of the application lies in the investigation of technical combustion processes in gas turbine combustion chambers. Combustion chamber systems from the field of energy generation as well as from aviation are analysed. Significant effects are analysed, taking into account fuel and load flexibility: in addition to transient combustion phenomena in turbulent flows, these include thermoacoustic effects and pollutant formation. This contributes significantly to the development of future technologies.
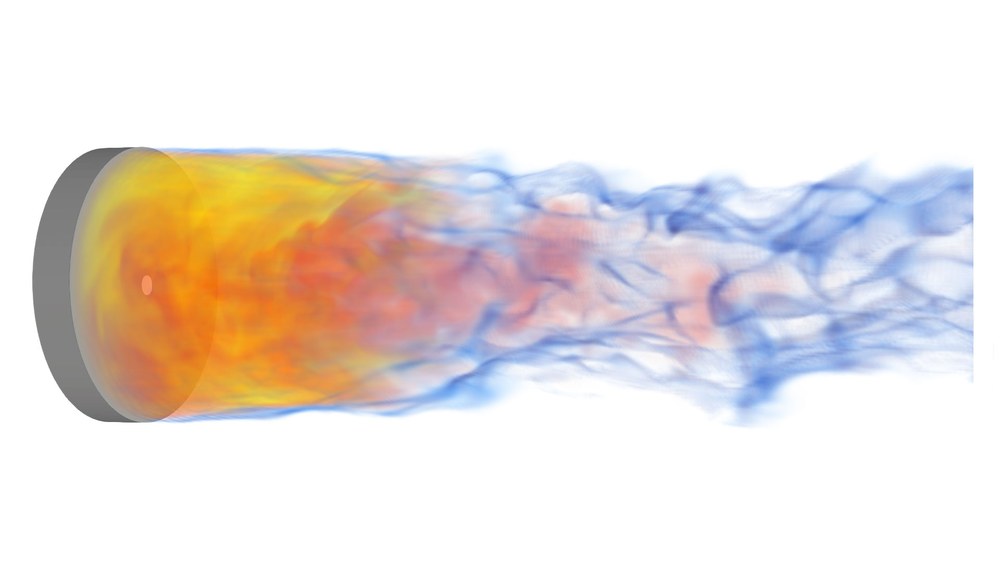
Calculation of soot formation with sustainable aviation fuels
For an accurate numerical representation of the physical and chemical processes in the flow, the department prefers to use the computational method "Large-Eddy-Simulation", in which the energy-rich parts of the turbulent flow are resolved directly. An essential prerequisite for the successful implementation of such simulations is the spatial discretisation of higher order on unstructured grids available in ThetaCOM, which makes it possible to calculate application cases with high complexity. In addition, there are detailed reaction mechanisms in combination with models for turbulence-chemistry interaction. Soot formation trends for regular and future sustainably produced fuels can be investigated with a proven model of high quality, that can calculate both the quantity and the size distribution of emissions.
There are many years of expertise and experience not only in the field of gas turbines, but also regarding the simulation of combustion in scramjets (supersonic combustion) and in rocket combustion chambers. With the in-house code TASCOM3D, corresponding transient flows with shock systems and supercritical thermodynamics can be calculated spatially and temporally with high accuracy.
For all in-house codes, the efficient use of the DLR's own high-performance computing infrastructure plays a major role in finding solutions for complex problems in a short time frame. Currently, excellent scalability is achieved consistently for both ThetaCOM and TASCOM3D when using several thousand computing cores.
The department also supports design calculations in the design process for micro gas turbines. Here, detailed investigations of individual phenomena play less of a role. Instead, it is important, for example, to calculate a large number of geometric variations reliably and efficiently with ThetaCOM as part of an optimisation using time-averaged conservation equations (Reynolds-Averaged Navier Stokes Equations - RANS/URANS).